Powerful intralogistics - Züger Frischkäse expands by 150 pallets per hour with two lifts from Westfalia
For the fourth time, Westfalia Logistics Solutions Switzerland has expanded the intralogistics at Züger Frischkäse - increasing the retrieval capacity of the entire system by 150 pallets to 400 pallets per hour and the fresh storage capacity by 700 pallet spaces. After the contract was awarded in March 2020, the western expansion of Switzerland's largest mozzarella pro-ducer and fifth-largest milk processor, which invested more than ten million Swiss francs, went into operation at the end of 2021.
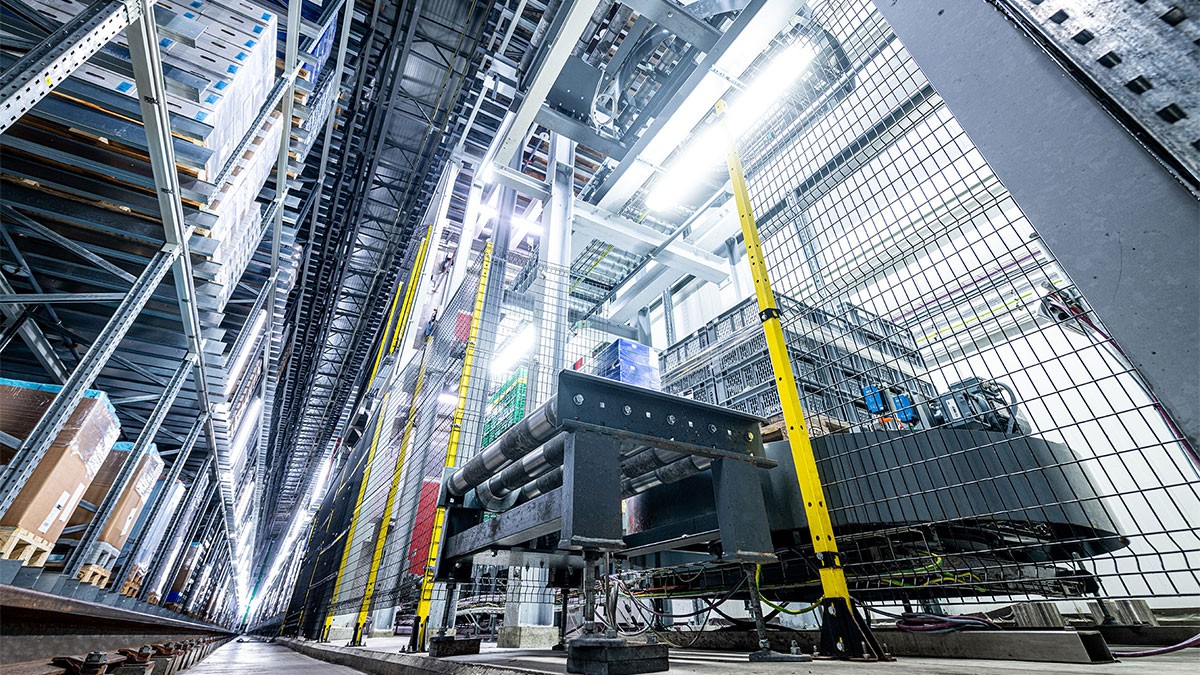
Fast storage and retrieval lines and two stacker cranes in a storage aisle create the necessary throughput for the ever-growing range of products at Züger Frischkäse. (Photo: © Westfalia Logistics Solutions Europe/Marcello Engi)
Self-supporting silo design saves costs for hall construction
Züger Frischkäse AG uses state-of-the-art technology such as a coagulator and comprehen-sive automation. 50 percent of the products are exported, the main customer being Germany. The farm processes between 400 and 450 tonnes of milk per day, approximately 20 percent of which is organic milk. René Giger from Westfalia Sales Switzerland has accompanied the company's intralogistics automation since 2006. In 2010, Westfalia's first order was the com-pact automatic fresh food warehouse with 2,500 pallet spaces. The intralogistics specialist has meanwhile extended this to the west with its fourth more extensive order. "We had to in-crease the throughput in order to run the growing number of products through the operation," says Giger, describing the challenge. "In addition, more packaging material had to be stocked to cushion rising prices, raw material shortages, availabilities and longer delivery times. The 700 additional fresh storage bays were a logical choice due to the compact layout." The self-supporting silo design saves costs for the hall construction.
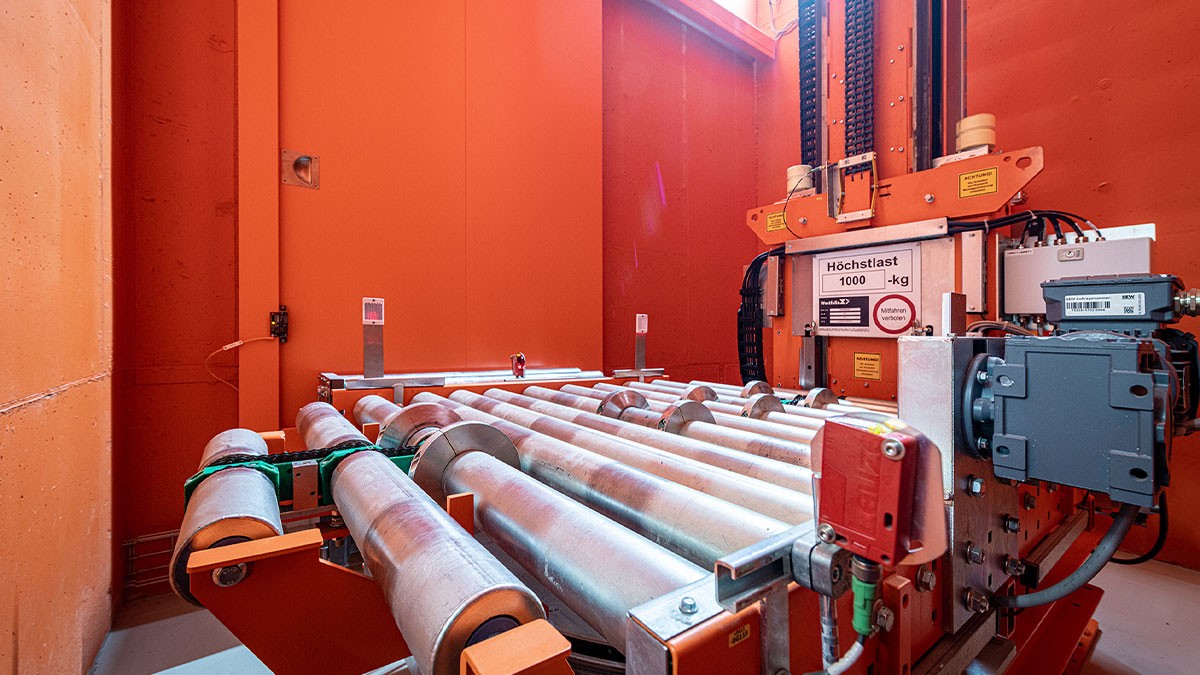
Two vertical conveyors connect all floors through turntables with roller conveyors. The system in-creases the retrieval capacity by 150 to 400 pallets per hour. (Photo: © Westfalia Logistics Solutions Europe/Marcello Engi)
Placed on the roof to save space
Six vertical conveyors (SKF) were previously used for the daily throughput of about 2,000 pallets. Giger: "We installed two more single-column SKFs and connected them on five levels with conveyor technology. The lifts are equipped with roller conveyors on turntables. Load units can be picked up and transferred from the front and side. The SKFs transport an addi-tional 150 pallets per hour at up to 90 metres per minute over a lifting height of 24.5 metres, thereby increasing the storage capacity from production and the packaging task.
The high number of vertical conveyors is a special feature of the storage system: "Because of the confined space, our storage technology with satellite was a must for the logistics solu-tion from the very beginning - we built all three warehouses on what used to be the roof," says Giger. This is because the particularly compact multi-depth storage units with up to five levels can be cut to fit tight spaces. "After the fresh storage of four degrees Celsius with 115 by 15 by 11 metres, we installed the frozen storage of minus 18 degrees Celsius with 30 by 24 by 11 metres and 1,400 bays in 2012. In 2014, the packaging warehouse followed with 40 by 34 by 11 metres and around 3,000 shelving spaces for pallets. This has enabled us to automate the company's internal logistics processes."
Doubled access frequency in the fresh food warehouse
The system is designed for wooden and plastic Euro pallets, for plastic pallet boxes and for load units up to 1.3 metres wide, 0.9 metres deep and 1.8 metres high. In the refrigerated and frozen storage facilities, they weigh up to one tonne, while the packaging material units weigh up to 250 kilograms each. Westfalia has installed all components of its storage systems, in-cluding its own programmable logic controller (PLC) and the key technology satellite, at Zü-ger, including two transverse transfer carriages for the picking zone. The four storage and retrieval machines (RGB) each transport 60 pallets per hour in double operation and are equipped with the chain satellite load handling device. In order to double the access frequen-cy in the fresh produce warehouse, two RGBs run on one rail. Each storage system requires only one aisle, reducing energy consumption and maintenance.
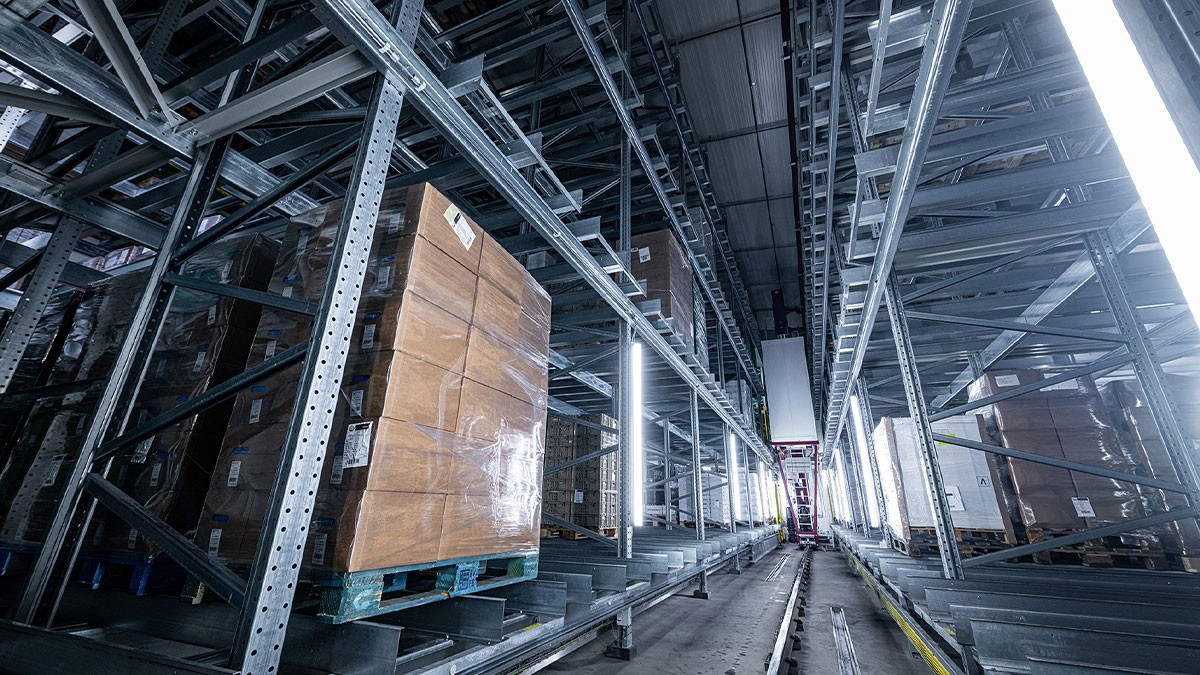
Pre-cut mozzarella sticks are stored in the deep-freeze warehouse, which are then defrosted in the customer country and used for sandwich production. (Photos: Westfalia Logistics Solutions Eu-rope/Marcello Engi)
Westfalia's Savanna.NET warehouse execution system generates up to 8,000 transport or-ders daily at Züger. It bundles warehouse management and warehouse controlling - "with all the project-specific features such as two SRMs on one rail or a vertical conveyor with two load handling devices on top of each other," explains Christian Goltermann, Sales Manager Software & IT at Westfalia. "It exchanges data with the CSB host system, automatically fills and empties a blast chill zone, supplies a pick zone and the three different product and tem-perature zones for fresh, deep frozen and normal temperature for packaging." In addition to the software, Westfalia implemented additional TERRA brand Savanna workstations as cli-ents of the CSB host system. A total of 20 workstations are distributed throughout the factory. The system was retrofitted with six monitoring scanners in order to exclude a data misalign-ment between warehouse management and the material flow computer.
Sustainable warehouse automation for higher productivity
The step-by-step expansion of the automatic storage system in a very confined space ac-commodates the company's development, explains Silvan Egger, the responsible project manager at Züger Frischkäse AG. "Although we realised the first warehouse back in 2010, we were able to upgrade, refit and update it. This expandability has great advantages for the company and its development. With the current expansion, we can dramatically increase productivity. Trucks no longer have to wait for their pallets," says Egger.
The long-standing cooperation has proven its value: "Because of the specific expertise, we have the best solution for us. This also includes a spare parts warehouse that is as simple as possible and components that remain the same as in previous years. We work with the same, long-standing Westfalia employees. It was possible to implement ideas and improvements in the current project. And we were able to superbly integrate the new system into the existing system." Egger therefore definitely recommends the intralogistics specialist.
Additional information and contact
Westfalia Logistics Solutions Europe GmbH & Co. KG
Frank Muscheid
Corporate Communications Officer
Tel. +49 5425 808 906
muscheid@westfaliaeurope.com
www.westfaliaeurope.com