We need open, modular and scalable automation
Mr. Winter, when you look back at automation solutions in 1980, what challenges do we face today? What are the key technologies?
Today, mechanical engineering is software development. This increases the development effort and requires appropriate skilled personnel. We've recognized that a completely new range of solutions is needed here than was the case 25 years ago. It must greatly simplify the world of automation and at the same time solve the challenges faced by customers. With ctrlX Automation, we've created a platform that overcomes the limitations of previous solutions. Basically, it's the "smartphone of automation".
Does that mean that creating software solutions is the biggest part of automation today?
The proportion of software in mechanical engineering is increasing. With ctrlX Automation, we're breaking through the traditional boundaries between machine control systems, IT and the Internet of Things. With the real-time-capable Linux operating system, open standards throughout, app technology for programming and comprehensive IoT connectivity, our platform reduces engineering costs by 30 to 50 percent. App technology in combination with openness provides our customers with the basis for developing new business models in order to maintain or expand their competitiveness.
This software orientation requires other skills and other tools that the professionals need to bring with them. How would you assess the current situation on the labour market?
The shortage of professionals in the field of software engineering is also affecting the packaging industry. One challenge, for example, is programming: More and more younger professionals are no longer exposed to the historically evolved automation languages according to IEC 61131 or G-code during their training. At ctrlX Automation, university graduates can quickly create customised solutions even without prior knowledge of these languages. They use the familiar high-level and scripting languages of their choice and create software in Java, JavaScript or Python, for example. Or they use low-code programming languages, C languages or the open source software Node-RED to realise individual functions.
What demands are placed on automation by the food production sector, for example in the area of packaging technology?
Consumer goods such as crisps and chocolate bars, as well as non-food products, have to be packaged and sold quickly and cheaply. Our platform offers almost unlimited room to manoeuvre and can provide support in many areas. The open complete solution supplies all hardware and software components for the control, regulation, monitoring and optimisation of packaging machines. It offers a modular overall system that networks, controls and orchestrates all components across the board.
All of this is supplemented by so-called apps. What's behind all this?
CtrlX Automation is based on powerful multi-core processors that can be used in an embedded controller or directly in the drive (ctrlX Drive). On the software side, this is complemented by apps that are available in the ctrlX Store to expand the functional scope of packaging machines as required. Users can now choose from solutions in 16 main categories and 150 use cases from 90 partner companies.
Can you give us an example of this kind of app?
Our ctrlX Motion app is highly scalable and covers all motion tasks in the packaging industry, from single-axis to synchronised multi-axis and robot movements. A ready-to-use, open application project in PackML (Packaging Machine Language) and the IEC 61131 standard combines various apps from the PLC, motion and HMI areas and offers users numerous advantages: Start of the first project in just ten minutes, up to 60 percent time savings in coding, increased reusability of the code, web HMI in responsive design and open source code.
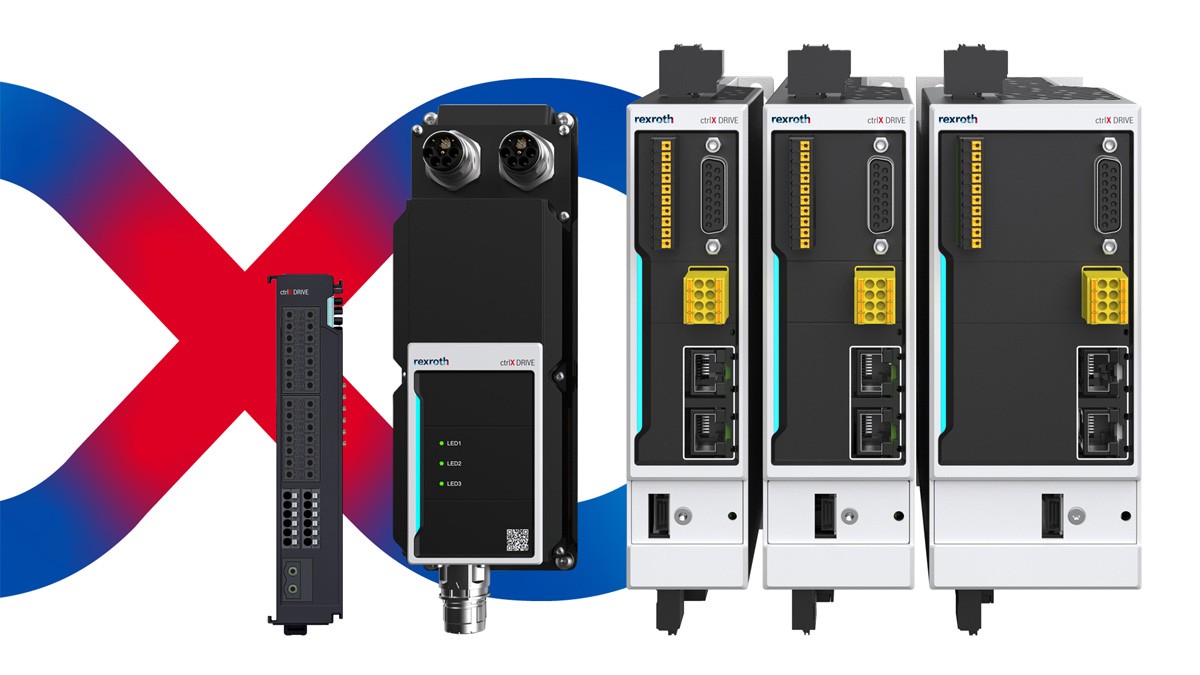
Our ctrlX Motion app is highly scalable and covers all motion tasks in the packaging industry, from single-axis to synchronised multi-axis and robot movements. A ready-to-use, open application project in PackML (Packaging Machine Language) and the IEC 61131 standard combines various apps from the PLC, motion and HMI areas and offers users numerous advantages: Start of the first project in just ten minutes, up to 60 percent time savings in coding, increased reusability of the code, web HMI in responsive design and open source code.
The Linux-based operating system ctrIX OS was originally developed exclusively for Bosch Rexroth hardware. In October 2022, you then announced that ctrIX OS would also be available as a separate solution. How do plant manufacturers benefit from this?
CtrlX OS has also been available as a separate solution for real-time use in industrial environments since 2022. It can be used at all levels, i.e. from the field level to the cloud level, as well as on a wide variety of hardware. The many networking options of the ctrlX Core control system as an edge device are also crucial for machine manufacturers, like Winkler and Dünnebier confectionery machines. They range from vertical interfaces in accordance with the Weihenstephan WS or PackML standard and direct data access by ERP and MES systems to horizontal communication based on OPC UA and the new "WS Sweets" language sub-area in the Weihenstephan standard.
The keyword here is cabinet-free drive technology: OEMs are increasingly demanding decentralised drives that support various field buses. How do you react to this?
In autumn 2023, we presented the third generation of cabinet-free drives. We are therefore serving a trend in automation, as future growth in the market for decentralised drive technology is particularly strong in sectors such as the packaging industry, intralogistics and food processing. As a pioneer of cabinet-free technology, our customers benefit from more than 15 years of market experience.
What advantages does the new generation of drives offer here?
Based on the ctrlX Drive, we offer a significant expansion in terms of scalability and topology for drives with IP65 protection. The drive system enables a high degree of flexibility thanks to the scalable number of axes, its single and double-axis design, various cooling concepts and much more. This allows different topologies to be implemented and adjustments to be made as required.
Energy efficiency also plays a major role, as food manufacturers are increasingly looking to reduce their carbon footprint
As a result, more and more energy-saving functions are being integrated into automation components - for example, our Smart Energy Mode in a servo drive. Among other things, this ensures that the energy is intelligently kept in the system and load peaks are avoided as far as possible. Extensive tools and models for energy and performance simulation make it possible to design systems in an energy-optimised way.
What insights can be derived from this?
Insights derived from simulation and analysis form the basis for maximising the efficiency of lines. The virtual testing of production concepts also means that fewer physical prototypes are required. This in turn reduces the amount of material used. But energy monitoring functions also help to increase efficiency in packaging machines. The ctrlX Core control system, for example, makes it possible to collect and analyse information from all machine components. Intuitive dashboards display processed data and statistics immediately.