Vacuum Saves Energy and Space
The Schubert Group, for example, has decades of experience in food packaging. The Crailsheim-based family business relies on a combination of simple mechanical systems, intelligent control technology and modularity for its digital, robot-based packaging machines. The company takes an interdisciplinary approach to sustainability through its Schubert Consulting division and the newly established Packaging Competence Center (PCC). Experts discuss materials and technologies, including their automation, in the context of legal requirements and the market.
Material usage
The Schubert Packaging Competence Center sees the main areas for optimisation in the sustainable packaging of baked goods as being in the material, with cardboard or mono films being preferred in terms of sustainability. At the same time, the goal is to make the best possible use of the templates during automated cutting using robot technology. The material thickness and properties should enable them to be processed on the existing machines wherever possible.
According to the Schubert, significant material savings can often be achieved in the long term by reworking the formats with smaller and simpler cuts or thinner trays. The same objective is behind a current idea of the Schubert experts for optimised multipacks of muffins or similar baked goods. Normally, this type of tray is cut and folded according to a template that includes the bottom and top with hole markings for the baked goods. In the three-dimensional design that the carton manufacturers are provided with, the cut-outs for the openings are bent downwards and therefore serve as a base support for the product moulds or cups. This eliminates the need for the material surface for an extra base. In addition to a material reduction of around 40 percent and less waste for the cardboard manufacturers, the latter benefit from a smaller carbon footprint for transport to the customer due to the lower weight, as Michael Graf, Director PCC points out.
An alternative to glued cartons
In the context of sustainable packaging methods, he also refers to the new Dotlock technology for glue-free carton production: Instead of gluing the corners with heated glue or folding them with a higher material consumption, the secret lies in a mechanical technique: Similar to the so-called clinching process used to join metal plates, the cartons are pierced from one side with several needle-like pins and the hole collars that protrude toward the rear are bent into a stable interlocking fit using pressure. The Dotlock cardboard solution is fully recyclable through the paper cycle, says Graf. However, cardboard-monofilm hybrid solutions, which could also be recycled, are possible as well.
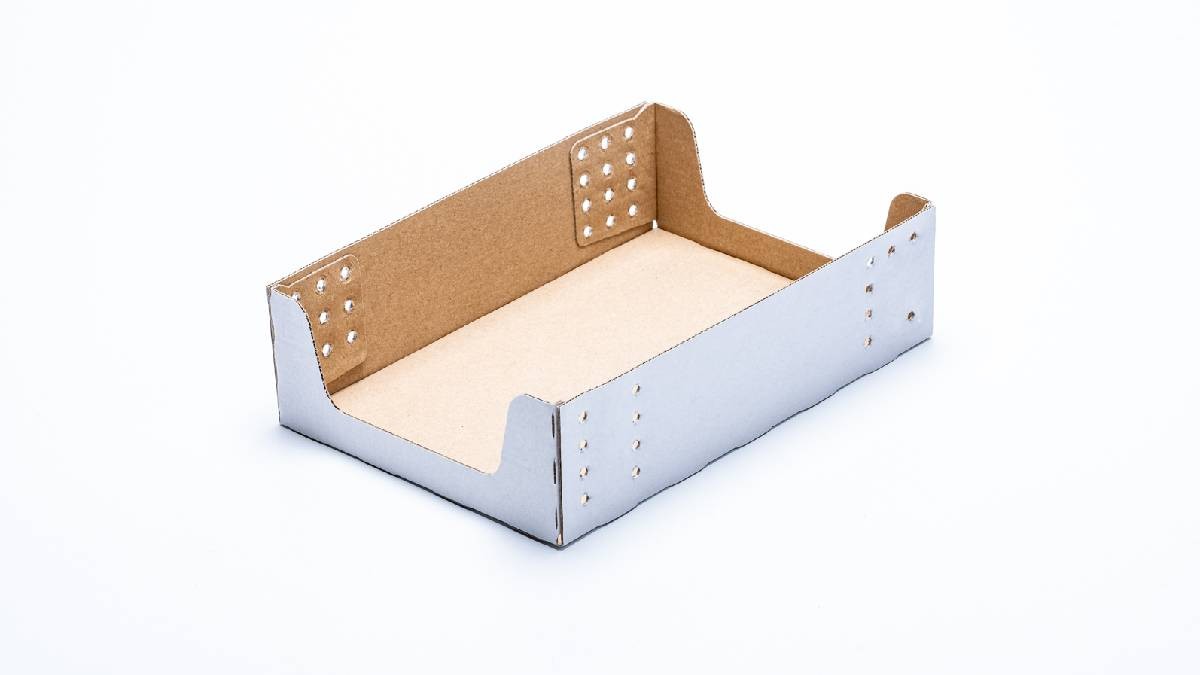
Alt Text: New dotlock technology for glue-free cardboard production. © Gerhard Schubert GmbH
Becoming more sustainable with less energy consumption
MULTIVAC, based in the Allgäu region of southern Germany, is also an expert in industrial packaging and other machines. Among other things, it has recently been looking at the aspect of saving energy when packaging freshly baked goods. After they come out of the oven, bread, pastries or small baked goods are usually first cooled down to ambient temperature using cooling spirals or in long cooling tunnels and then film-wrapped. With the innovative new Cooling@Packaging system from MULTIVAC, both steps are instead carried out hygienically and in combination in a single machine.
In this process, loading robots position the products, which are at a temperature of approximately 95°C directly out of the oven, into preformed thermoformed packs. A vacuum is then applied to the chambers, causing the moisture contained in the food to escape. The evaporation energy that is released at the same time cools the food down to 30°C within a few seconds. Product manager Thomas Fickler explains the process in more detail: the packages are vacuum-packed in several chambers between the forming and sealing stations. The number of Cooling@Packing stations depends on the product and the output. In the last chamber before the heat-sealing station, the final vacuum is around 20 mbar.
According to the company, the process is suitable for the high-performance segment, and users can continue to use their standard packaging materials such as PA/PE films. Cooling&Packaging, which won the German Packaging Award from the German Packaging Institute (dvi) last autumn, is about to be launched on the market. As Fickler said when asked, in principle the approach could also be applied to other foods. However, this would have to be specifically verified with tests.