Three Steps to Digitalised Food Production
First step: Record machine data
Sustainable process optimisation begins with the comprehensive collection of data. However, companies in the food industry in particular often face challenges such as the heterogeneity of their machine landscape or the integration of existing systems into a digital environment. Data collection presents companies with the following challenges:
- Old machines: Older systems often do not have digital interfaces or standard protocols that enable seamless integration.
- Data diversity: Different machine types and processes generate heterogeneous data (formats) that are difficult to standardise.
- Sensitive data: The increasing networking of machines increases the risk of data and therefore know-how theft and the risk of external interference through hacker attacks.
In addition to increasing efficiency, compliance with legal requirements is a decisive factor. HACCP (Hazard Analysis and Critical Control Points) conformity particularly plays a central role in food production. This requires the continuous monitoring and documentation of critical control points, such as temperature or pressure, to ensure product safety.
This is where Manufacturing Execution Systems (MES) come into play. These systems make it possible to record data directly at the source, consolidate it and make it available centrally. gbo datacomp GmbH from Augsburg, an IT system house, has specialised in the development of such MES solutions and offers technologies that efficiently integrate even complex machine parks.
"The equipment of machines is often varies greatly. That's why we rely on flexible interfaces such as OPC DA, OPC UA, MT Connect or sensors to integrate virtually all machines into an MES system at a reasonable cost," explains Michael Möller, CEO of gbo datacomp GmbH.
- OPC DA (Data Access): Older standard for real-time data exchange, suitable for older machines.
- OPC UA (Unified Architecture): Modern, platform-independent standard for secure, flexible data exchange.
- MT Connect: An open standard for the standardisation of machine data, which is particularly widespread in production technology.
In addition, companies must ensure the protection of sensitive data. Access rights, encryption and secure networks form the basis for secure data processing. "A holistic approach is crucial: Data protection guidelines, regular data checks and employee training increase security in a networked production environment," emphasises Michael Möller.
Second step: Analyse data
Data alone does not offer any added value – valuable insights can only be gained by analysing it. Modern technologies such as AI and machine learning are opening up new opportunities to better understand and improve production processes. These technologies make it possible to recognise anomalies in production data and predict their impact on product quality.
Data analysis applications:
- Predictive maintenance: With the help of predictive models, companies can monitor the condition of machines and systems and recognise potential problems at an early stage. This minimises unplanned downtime and optimises maintenance intervals, significantly increasing efficiency.
- Real-time monitoring: MES systems visualise important key figures such as OEE (Overall Equipment Effectiveness) or reject rates so that companies can maintain control over their production at all times.
- Networked systems: Standards such as OPC UA enable the seamless integration of data from different machines and systems into a central database.
But a machine learning model is only as good as the data used to train it. Inaccurate or incomplete data can lead to incorrect results. Careful data preparation and standardisation are therefore essential for ensuring reliable analyses.
Third step: Optimise processes
The findings from the data analysis form the basis for targeted process optimisation measures. In particular, innovative technologies such as digital twins play a key role here.
The digital twin is a virtual image of an actual process. This allows scenarios to be simulated and parameters to be adjusted without disrupting actual production. This is particularly valuable in food production, as biological processes such as fermentation are often difficult to control.
The digital twin therefore offers an opportunity not only to better understand production processes, but also to optimise them in a targeted manner. Practical experience shows how companies can achieve measurable success with digital technologies and MES systems. Two practical cases from gbo datacomp GmbH illustrate the potential of digitalisation:
- Series manufacturer in the metal industry: Machine downtimes were reduced by 15 % through the introduction of an MES, which also increased productivity by 15 %.
- Manufacturer of rubber solutions: Digitalisation of the vulcanisation process increased productivity by 33 %. The increased transparency of boiler statuses enables operators to quickly recognise which machine requires their attention. This allowed employees to manage several systems at the same time without compromising efficiency. The machines were optimally utilised, while the documentation of quality features took place automatically. Deviations and trends were visualised online so that operators could intervene at an early stage before major problems arose.
Conclusion and future prospects
The digitalisation of food production will continue to progress in the coming years. AI, machine learning and IIoT (Industrial Internet of Things) solutions will play a central role in this, as they enable the processing of huge amounts of data and the protection of sensitive information.
Platforms such as Manufacturing-X are creating new approaches for decentralised data ecosystems, while automation and robotics are further increasing the demands on MES systems. At the same time, sustainability, knowledge management and resource-saving production methods are driving the need for precise production data.
Digitalisation offers enormous opportunities for food production - from increasing efficiency and reducing costs to ensuring quality. Companies that consistently implement the three steps - collect, analyse and optimise data - not only create future-proof production, they also gain decisive competitive advantages. Those who act now will benefit from the advantages of these technologies and actively shape the transformation of the industry, emphasises Michael Möller.
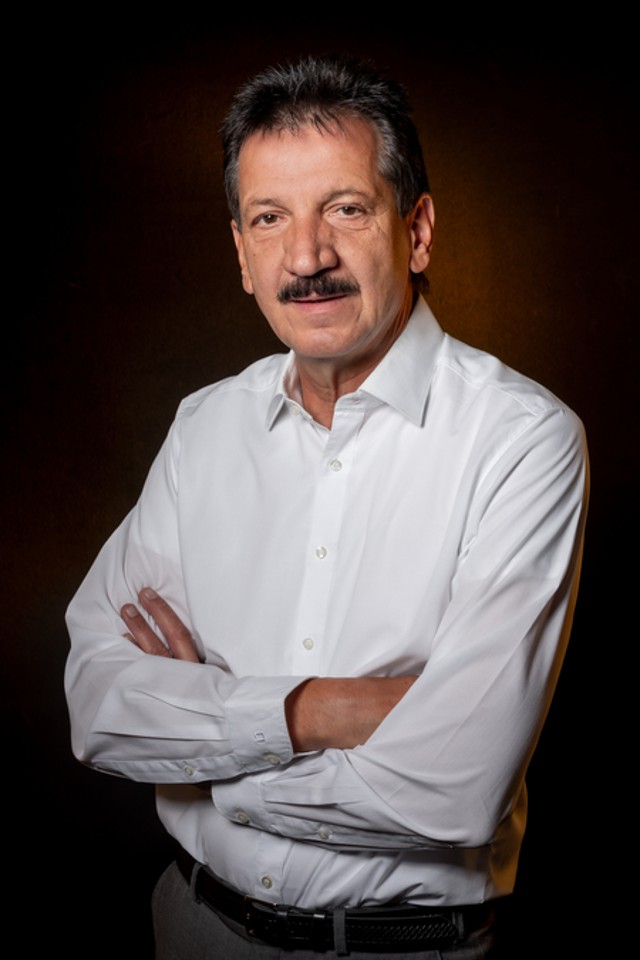
©gbo datacomp GmbH
For further information please contact:
Michael Möller
CEO
gbo datacomp GmbH
86150 Augsburg
Germany
E-mail: m.moeller@gbo-datacomp.de
https://www.gbo-datacomp.de/en