The Future of Valve Technology
Software localises defective filling valves
Process valves are used in numerous applications in the food and beverage industry. Nevertheless, the continuous maintenance and control of the valves and their sealing elements is often still based on visual inspection. However, what the market demands in times of increasing automation is the use of inspection technology that identifies problems and defects before they cause equipment to break down. A digital management system offers a whole range of advantages in the area of condition monitoring – from minimising downtime to the option of shutting down individual valves without interrupting production. The Innocheck MMS from KHS is an example of this type of application when filling and sealing cans. It localises defective filling valves and closure elements and evaluates these by means of a precise readout of complete parameters. "Based on the evaluation, bottlers can trace defective fillings back to individual valves and intervene at an early stage," explains Henrik Kahrmann from Product Support Labelling and Inspection Technology at KHS.
Comprehensive condition monitoring
The latest generation of condition monitoring systems is able to detect even the smallest changes in condition even earlier than before. The use of advanced sensor technology plays a key role in this. It continuously monitors parameters such as temperature, humidity and air pressure. These are transmitted via existing communication interfaces so that they can be specifically analysed for anomalies or emerging negative trends. This makes it possible to detect a deterioration in the condition of the device and operating conditions long before an actual fault occurs.
The control air supply pressure is one of the most important parameters for pneumatically actuated process valves. It is still one of the main causes of errors in valve operation. If it is monitored specifically, it is possible to see immediately whether it is too low, too high or unstable. Gemü, the valve technology specialist, is taking this approach with its new Leap Lean product generation. A central component is the 12A0 – an intelligent electrical position indicator with integrated Hall sensors. They record parameters such as humidity and operating pressure. In addition, the 12A0 offers the latest communication interfaces such as ASi-5 and IO-Link. The sensor values can be displayed directly on a smart device using the Gemü app and a Bluetooth connection. This should make troubleshooting much easier in the event of a fault and also provides the option of directly reading the current condition of the valve during maintenance or service work.
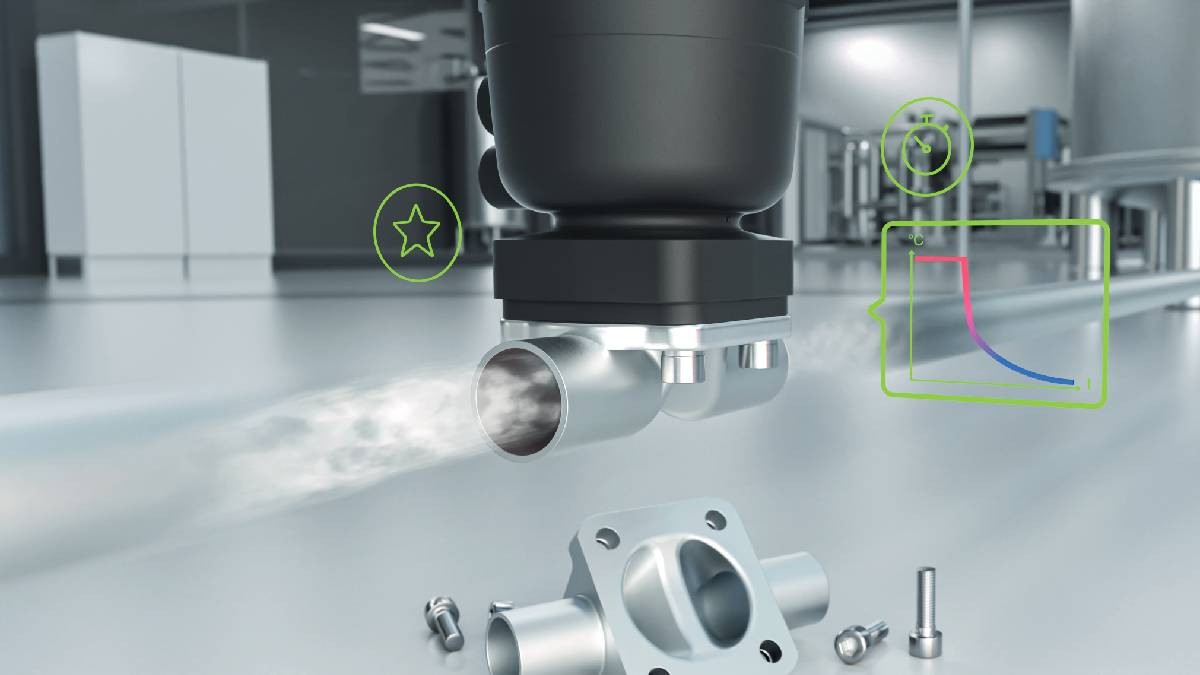
The tube-formed housings have a significantly lower thermal mass than forged or cast variants. This advantage becomes more pronounced as the nominal diameter increases. © Bürkert Fluid Control Systems
Plant availability in terms of sustainability
A lean cabling system and the use of intelligent control attachments for process valves, which are, for example, integrated via IO-Link, also ensure better system monitoring for Bürkert solutions while simultaneously reducing installation costs. However, wherever systems are optimised for high availability, sustainability and the lowest possible operating costs are also important. All components installed and involved in the processes must contribute to this. In SIP processes in particular, large quantities of pure steam are needed to bring the massive valve bodies up to the sterilisation temperature. At the same time, the time during which production can take place is reduced because the housings heat up and cool down only slowly.
The developments of the fluid power experts from Ingelfingen include a tube-shaped housing with a considerably lower thermal mass. "Since SIP processes allow for significantly faster heating and cooling than conventional forged or cast housings, less pure steam and energy is required to bring the valve bodies up to sterilisation temperature," explains Michael Wiedmann. At a temperature difference of 100 degrees Kelvin, energy savings of over 50 percent can be achieved per SIP cycle. Assuming an application with 100 valves, that saves 875 kilograms of carbon dioxide per year,’ says the product manager for diaphragm valves at Bürkert Fluid Control Systems.
Robust lightweight
The basis for this is provided by the special manufacturing process: The diaphragm valve bodies are manufactured using a tube forming process, also known as hydroforming. This means that a metallic tube is formed into a valve housing in a closed mould using internal pressure in several steps, including heat treatment. For example, the same pipe materials that are used and approved in the plant can be used for the valve housings. Furthermore, assembly or welding operations like those required for a half-shell construction are no longer necessary, and the housings weigh little more than a tube of the same length. In contrast to cast housings, no shrink holes or other impurities occur during production, avoiding the risk of contamination or production waste. Another plus for cleaning: Nothing can accumulate due to direct pipe-to-pipe welding.
Less stress for the diaphragms
At the same time, the productivity of the plant increases because the fast heating and cooling process shortens the non-productive times for cleaning. The more often cleaning is required, the more the user benefits from it. As the valves heat up and cool down faster during the SIP process due to their comparatively low thermal mass, the thermal stress on the temperature-sensitive diaphragms is also reduced. They last significantly longer than is usual with other types of housings. Depending on the application, their lifespan can be more than doubled, which extends the necessary service cycles and also contributes to sustainability.
Wiedmann is convinced that "in the end, the diaphragm valves in the tube valve body also offer the plant manufacturers a benefit that should not be underestimated." This is because: 'Unlike forged or cast housings, in most cases they don't need to provide additional support for the valves. This can significantly simplify the design and assembly and save labour, which therefore also reduces costs.
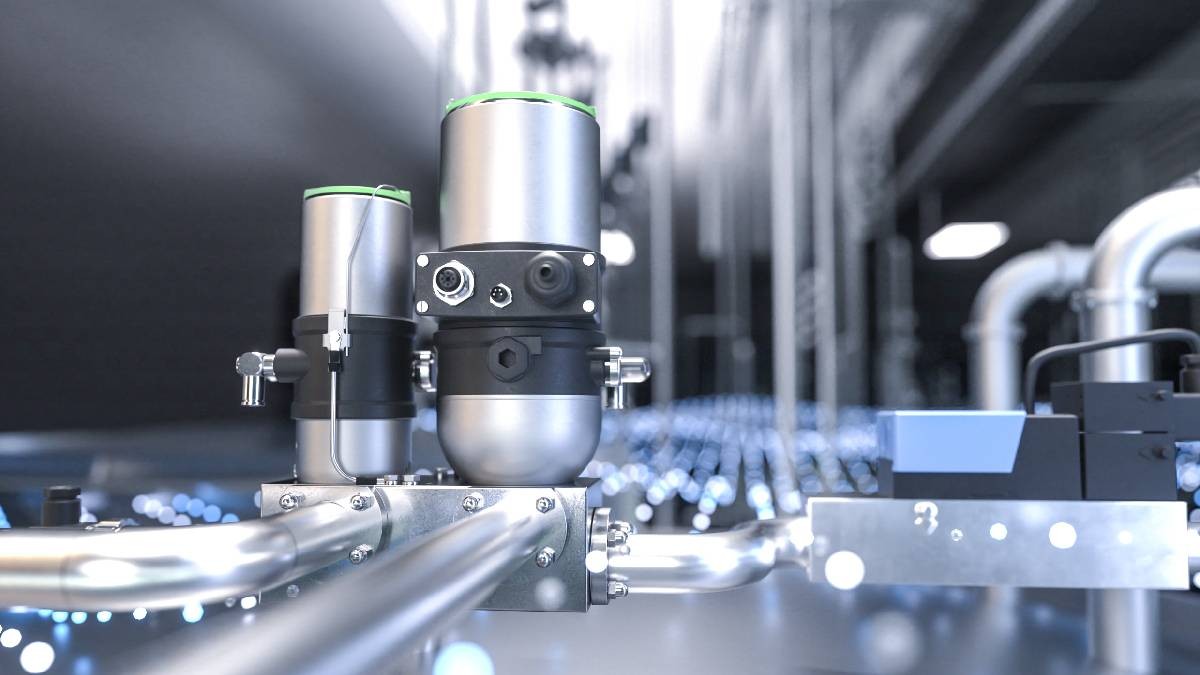
CBürkert supports users from the planning to the commissioning of their infrastructure for the automation of fluidic control loops. © Bürkert Fluid Control Systems
Data logging for process control valves
Bürkert valves are also used in process control to regulate the flow of liquids or gases. Bürkert offers automated data logging for valves that are used, for example, to control the process temperature. This makes it possible to identify optimisation potential faster and more cost-effectively, which reduces maintenance costs, prevents plant downtime and saves service technicians the need to travel. A pre-configured logging module is attached to the service interface of the control system for a certain period of time and then sent to the Technical Service department for analysis. With a mobile internet connection, it is possible to transfer the data directly to the analysis cloud. A mobile router connects wirelessly to the cloud and is attached to the control system with a bracket. This also allows the fluidics experts to realise individual solutions for automated data logging.
A product is developed based on experience
The inspiration for the development of the new service was a real-life scenario: A process control system with an element seat valve was used to control the temperature in a plant. The valve drive wore out in a disproportionately short time, which became noticeable through leakage to the outside. This meant that the entire valve drive had to be replaced. The system was therefore down more often, with each replacement costing money and resulting in a loss of medium. In the search for the cause, a member of the service team logged the data on site using a laptop. The analysis showed: A poorly adjusted controller was to blame. It constantly made barely noticeable adjustments, which led to wearing of the spindle seal. The parameters were adjusted accordingly during a service call, significantly extending the service life of the control valve. This experience was the initial motivation for the fluidics experts to develop automated data logging. To make data collection and troubleshooting easier, they developed automated data logging in its various forms. No intervention in the control system is necessary for this and the properties of the control valve remain unaffected.