Self-optimising process automation in breweries
Rotoramic system
The Rotoramic systems from GEA are based on an innovative dynamic filtration process involving rotating ceramic membranes. Thanks to their lower operating pressures, they require less energy compared to conventional cross-flow membrane filtration systems and are easier to scale, with the result that this technically very complex yeast filtration process can be controlled cost-effectively not only at large, but also at medium-sized and small breweries. Since the brewing industry in Germany is characterised by a comparatively large proportion of small and medium-sized breweries, this innovative technology can make a significant contribution to resource efficiency, especially for agricultural raw materials.
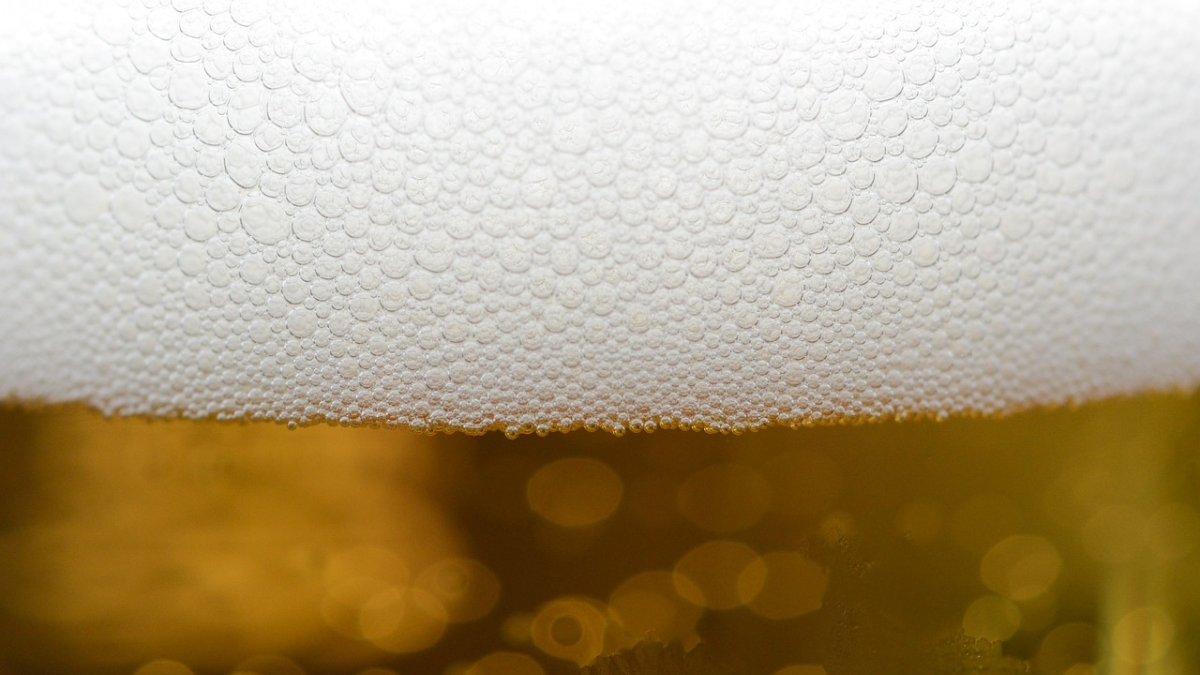
Rotoramic-Anlagen
For efficient and continuous operation of the Rotoramic systems, the filtrate and retentate outflows as well as the unfiltrate inflow and its concentration must be adjusted automatically, whereby an unknown unfiltrate suspension of initially variable quantity and quality is present in the brewing process. The thus far conventional process design, management and monitoring do not enable the full exploitation of the technology’s achievable potential, which is necessary for cost-effective implementation at small companies. Among other aspects, this concerns the mean filtrate volumetric flow (flux), the energy costs, the service life up to the cleaning cycle or the so far incompletely continuous operating mode due to backflushing.
The objective of the proposed project is to optimise the process and the Rotoramic systems’ process automation using Industry 4.0 methods in order to achieve:
- The highest possible yield and quality of the recovered beer
- A long membrane service life
- The most energy- and resource-efficient operation possible
Further information: www.ife-owl.de/en