Robots and No-Code Platforms in Intralogistics
Incoming goods with AI
Whether incoming or outgoing goods: Smooth processes play a decisive role in intralogistics both inside and outside a company. The entire process, as well as workplaces, conveyor systems and storage areas, should be designed in such a way that goods can be handled quickly and efficiently. Powerful AI functions can simplify these processes. This is because advances in the field of machine learning and the ever more powerful interpretation of camera data are increasingly enabling systems to react to changes in their environment in real time. Sick demonstrates this with two sensor solutions with integrated AI functionality: The Inspector83x 2D vision sensor for inline inspection tasks in high-speed production lines and the MIDS for automatic completeness checks in packaging processes. Another solution is the Palloc robot guidance system, an AI-supported, adaptive localisation solution for automatic depalletising with robots. It combines a powerful 3D snapshot camera with a pre-installed and pre-trained neural network and a new deep learning-based localisation algorithm.
Another new feature is the "Incoming Goods Suite" for automated goods receiving. Based on a digital platform for collecting, processing and providing package-relevant data, it enables transparent and efficient handover processes for incoming goods. Even the highest parcel volumes are to remain safely manageable with the Incoming Goods Suite. The scalable complete solution is available in scalable degrees of automation to meet individual requirements for the identification and sorting of consignments for incoming goods.
Picking robot with intelligent gripper system
All this shows: In addition to software experts and robotics specialists, the topic of AI is also attracting more and more intralogistics providers. Another example is the piece-picking cell from SSI Schäfer. It is a joint development with the subsidiary Rober. Equipped with AI object recognition and innovative gripper technology, the system ensures gentle handling during order picking. The integrated software recognises the individual parts reliably and error-free and determines the ideal gripping point, enabling the items to be deposited in a space-saving manner. Instead of finger-shaped grippers, compact suction cups are used for pick & place. Each item is placed as close as possible to the bottom of the container or carton. In addition: Using machine learning methods, the system is constantly learning and building up an extensive knowledge database.
Object detection via AI
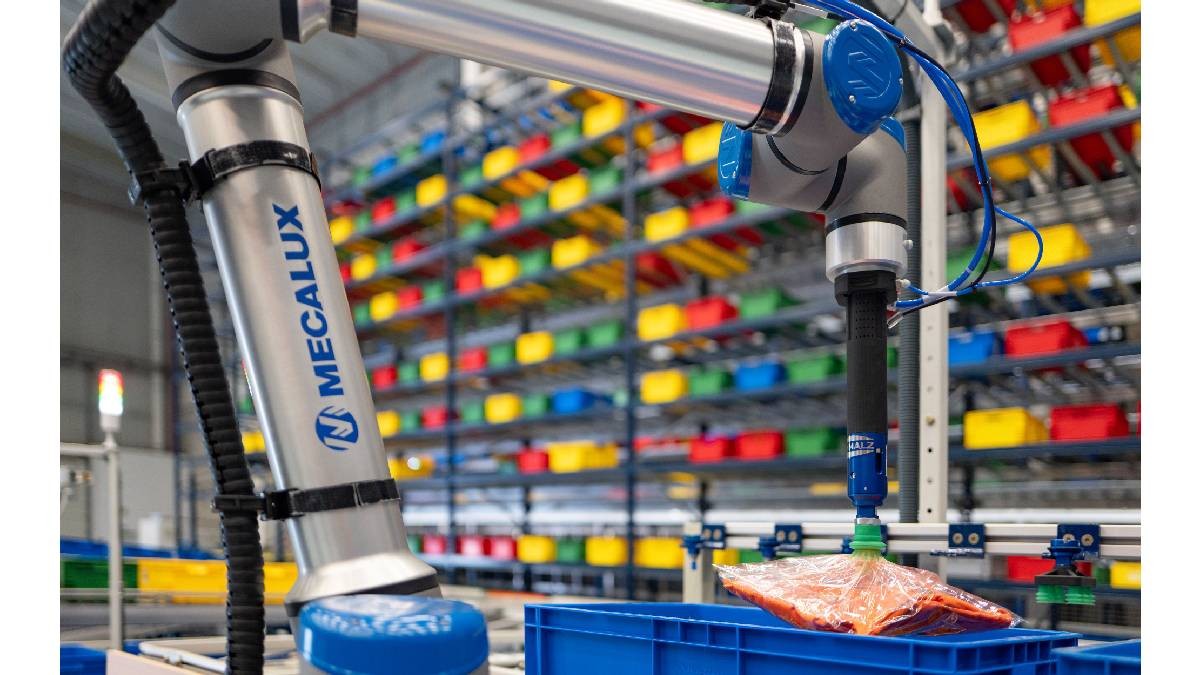
The Simatic Robot Pick AI 3D image processing software enables robots to pick any item in warehouse picking tasks, regardless of its shape and size. © Siemens
Siemens is also equipping order picking robots with AI technology. For example, Simatic Robot Pick AI enables robots to pick any item regardless of its shape and size. A pre-trained deep learning algorithm controls this ability to identify 3D positions for removal. The calculation of reliable removal poses ensures high throughput without collisions. Simatic Robot Pick AI also offers seamless integration into the TIA Portal automation platform. The Simatic Robot Library can be used to establish standardised communication between robot and PLC systems. Mecalux has launched two collaborative picking solutions based on Simatic Robot Pick AI: A cobot that is programmed to safely share the workplace with the operators and another cobot that works autonomously in high-performance picking stations. The solution is designed for 24/7 operation with up to 1,000 picks per hour. A camera positioned above the cobot's picking box takes a 3D image of the goods in order to compile the orders. As soon as the item has been selected, the cobot places it in the box with high precision, making optimum use of the available space. A specially developed algorithm ensures that the cobot places the goods in exactly the right place. With the help of Mecalux's warehouse management software, the collaborative picking solution can automatically change its picking system depending on the type of goods. After receiving a new box, the image processing system and the AI algorithm identify the items it contains. Both determine the most suitable way to pick each product. Both cobots carry out order picking completely autonomously and with maximum accuracy. "This allows the effects of the labour shortage to be cushioned while at the same time increasing operational efficiency in the warehouses," explains Dr Alexander Bollig, Vice President for Intralogistics at Siemens Digital Industries.
More efficient with no-code apps
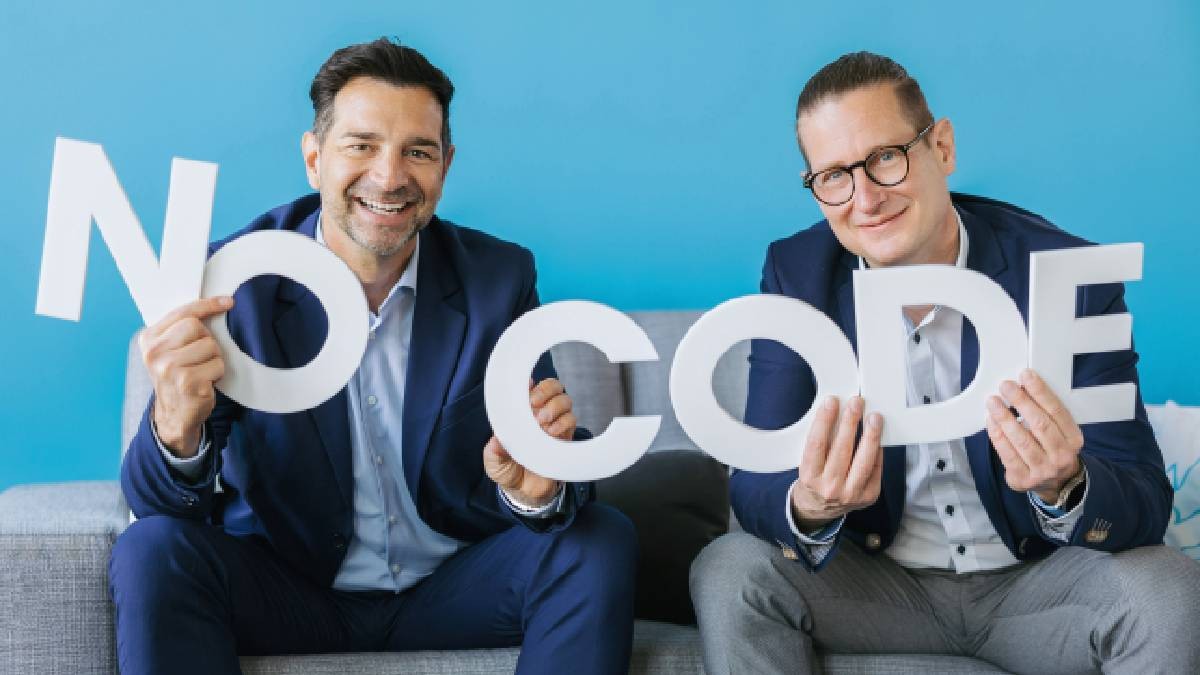
For Sven Zuschlag (left) and Thomas Schwarz, the incoming goods process is a suitable application for no-code platforms. . ©Philip Loeper
However, experts not only see great potential for digitalisation in recurring intralogistics activities such as order picking. If Sven Zuschlag and Thomas Schwarz have their way, all documentation that is still handled manually in analogue form today will also be processed via apps in future. The best example is the incoming goods department. If this is carried out via a tablet or smartphone, the recorded data can be seamlessly transferred to subsequent processes. Technically, the approach of the two smapOne founders is based on the generative AI GPT, which enables users to develop app prototypes with simple prompts, i.e. text instructions or process descriptions. Instead of building an app piece by piece from building blocks based on no code, a fully functional template is created from the prompts entered, which then only needs to be customised in its details. "The integration of AI into our no-code platform leads to an immense increase in efficiency, allowing users to develop customised digital applications even faster and more easily," explains CEO Sven Zuschlag. "Basically, text-to-smap is a creative solution that further lowers the barrier to creating apps, thereby paving the way for innovative business applications for an even broader user base."
A business app in just a few seconds
An app prototype generated with AI only takes a few seconds to complete. This makes it immediately clear whether one's own idea is viable and where there is a need for optimisation. Digitalisation measures can be implemented quickly in this way. Thomas Schwarz sees a further advantage in the domain knowledge of large generative AI models: "AI not only takes care of the technical implementation of app development, it also provides a whole host of practical process knowledge and best practices," says the CTO of smapOne. "As a result, users benefit from the AI's knowledge of processes or regulatory requirements, which are automatically incorporated into the creation of the app. Thanks to the significantly reduced research effort, development cycles are shortened and projects are realised in a matter of moments. It couldn't be quicker or easier!"