Reusable for Transport
In pooling, providers supply pallets, pallet boxes and containers for production processes, transport and the storage of food on a rental basis. In addition to reducing the number of empty runs and personnel costs, a system of this kind also includes the management of loading equipment, as well as cleaning and maintenance. The goal: Effective logistics processes, sustainable delivery routes and greater efficiency for optimised supply chain management. The containers and pallets used for pooling are designed to be particularly robust and durable. The plastic pallet Euro H1 from Craemer is a prime example of this. It is made of food-safe polyethylene and can be used anywhere in the entire logistics chain – whether in automated systems, when using forklift trucks, in high-bay warehouses or for storage. Even with intensive use and an increasing number of rotations, the pallet retains its shape. In addition, the robust carriers can withstand temperatures of minus 30 to minus 40 degrees Celsius, and briefly up to 90 degrees Celsius. They are available with RFID transponders for seamless tracking if required. In addition: When the products have reached the end of their useful life, they are 100-percent recyclable. Creamer takes them back and uses them to make new high-quality plastic pallets and containers in its own extruder and injection moulding machines.
They are designed to be recyclable and are intended for multiple use – both aspects that will take on a new significance with the new requirements of the Packaging and Packaging Waste Regulation (PPWR), which is expected to apply to packaging from 2026. As part of the European Green Deal, the regulation aims at reducing packaging and packaging waste and making it more environmentally friendly. For example, 40 percent of packaging in the EU is to be reusable by 2030, with this target rising to 70 percent by 2040. The entire industry is therefore faced with the challenge of finding sustainable solutions.
Everything from a single source
Chep is also continuously working on circular products designed for multiple use. With its solutions, the pooling expert helps companies to achieve their sustainability goals based on the "Share & Reuse" principle. A wide range of products ensures the hygienic, safe transport of packaging materials, ingredients and raw materials directly into clean production areas. For dry or solid ingredients, manufacturers can use dry IBCs in addition to plastic pallets. Liquid IBCs with different liners are available for transporting liquids. All solutions fulfil the strict food safety requirements. The risk of cross-contamination and the danger of product damage during transport is minimised. Thanks to their consistent quality and standardised dimensions, plastic pallets can also be used in automated environments.
The logistics provider takes care of cleaning, inspecting, repairing, delivering and collecting the containers and load carriers, and supplements these services with various supply chain services. "Our pooling model offers everything from a single source and is completely transparent. Hidden costs such as the return transport of pallets or the removal of product residues in IBCs, which drive up the total cost of ownership (TCO), are completely eliminated with our model," says Nicholas Gibbons, General Manager of Chep Inbound Solutions Europe. The logistics solutions for incoming goods are pooled by the Service Center in Gernrode, Saxony-Anhalt, Germany. Customers in western Germany receive the same service from the Zevenaar branch in the Netherlands.
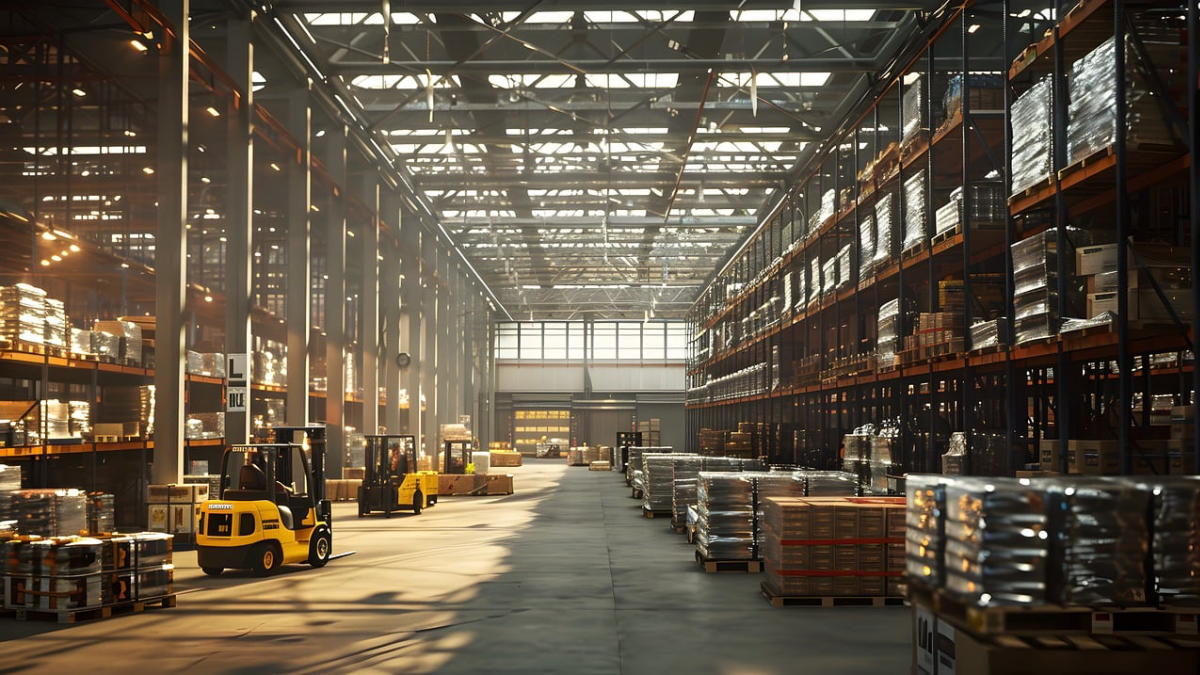
© Pixabay
Calculating the environmental impact
The environmental impact can be calculated even before switching to a pooling system. Chep uses the TCO tool for this. Based on a company's specific supply chain processes, it calculates the savings that can be achieved by using reusable plastic pallets and intermediate bulk containers (IBCs) compared to previous solutions. In addition, CHEP offers a life cycle analysis (LCA). The ecological footprint is determined, for example, by using reusable Chep pallets compared to disposable alternatives. The calculation is based on a specific period of time and is carried out in accordance with the ISO 14040 and 14044 standards, which provide a comprehensive, standardised methodology. The LCA has recently been adapted to determine the environmental footprint of liquid IBCs. In contrast to its TCO tool, this measures the environmental impact throughout the entire life cycle: from the resources used to manufacture a liquid IBC, through its use phase, to its final destination at the end of its life cycle. The TCO calculation and the LCA analysis provide manufacturers with sound arguments for prioritising reusable solutions in their inbound logistics for cost and environmental reasons.
Foldable for greater efficiency
With the foldable ZirConic container, Chep wants to offer another solution for a consistent orientation towards the circular economy. The large container is made from 97 percent of its total weight from post-consumer plastics and is therefore expected to set a new standard for sustainability. It is tailored to the needs of the packaging, e-commerce and co-packing industries and ensures greater efficiency thanks to its larger capacity and maximum foldability. Chep offers the container through its pooling circuit service. The foldability of the container increases the transport capacity for empty containers and improves efficiency in pooling. What's more, the load carrier's optimised loading capacity of 708 litres and 750 kilograms ensures greater transport efficiency. Digitisation of the ZirConic container makes shipments visible in their respective supply chains. The data collected provides information about the location of containers, usage patterns and turnover times. A life cycle analysis of CO2 emissions can also be used to determine how much a company can save by switching to this container.