Packaging module from KHS for switching from film to paper
Wrapping in paper has become the new trend
While paper may be relatively new as a packaging material on the beverage market, fillers are exhibiting constantly increasing interest in this material, particularly as an alternative to plastic film. KHS has therefore been offering the option of wrapping beverage cans in paper on its packaging machines since 2020. The function has been integrated into a combination machine in order to provide customers with maximum possible flexibility. No matter whether a wrap-around, tray or pad, with or without film wrapping or wrapping in paper – this system solution can process a wide variety of secondary packaging.
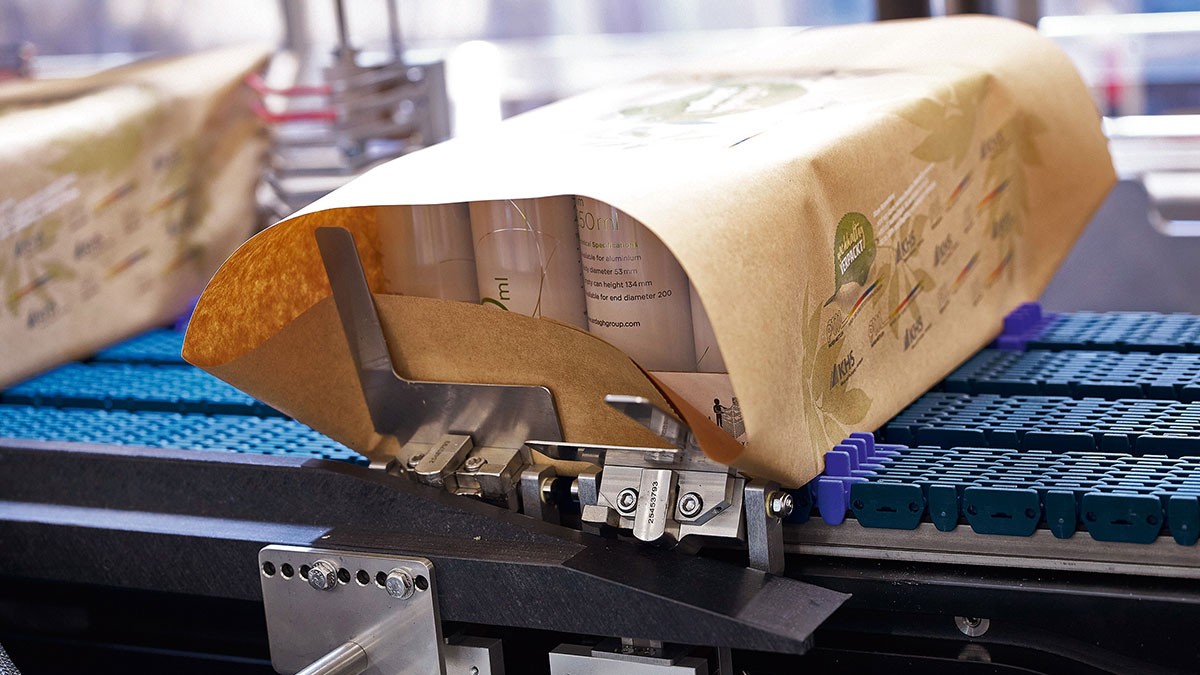
With paper wrapping, KHS is aiming to meet the demand for environmentally-friendly packaging materials. (Photo: © KHS)
Extension or replacement
Whoever does not wish to invest in new machines can retrofit the packaging solution as an additional option for existing Innopack machines. In this case, the machine is adapted for paper wrapping and extended with the necessary paper folding/gluing module. If paper wrapping is to permanently replace the previous use of shrink film as secondary packaging, two modules have to be exchanged. The wrapping module for previously processing film is then replaced with a further-developed module that is able to process paper. The shrinking tunnel is exchanged for a component that folds and glues the paper.
Unproblematic conversion with modular design
Once the modules are installed, switching materials does not necessitate any conversions other than the standard format change. As soon as the packaging material has been exchanged and the hot-melt devices are operational, production can start. “Conversion is unproblematic on all Advanced series machines”, explains Uwe Bartholemy, Head of Technical Support Packaging in the KHS Service Division. This is made possible by the modular design of the Innopack machines. “Generally, we can also convert older models, too. To do this, we look at each case individually in order to check, for instance, whether we need to update the control system.”
Environmentally-friendly packaging targeted
In addition to modern filling technology and digital solutions, KHS is consistently working on saving material as well as using more recycled content, thus sparing new resources. Customers worldwide benefit from over 40 years of expertise in the field of plastic containers for beverages, liquid food and home care products. The full-service supplier is also bringing its know-how to bear in the area of secondary packaging. Processing film made of up to 100 percent recycled material is therefore equally as possible as using paper or cardboard.