Minced meat in flow packs
Tradition in the third generation
As a family business rooted in the region, Feneberg Lebensmittel GmbH stands for quality and trust. "The regional production of food and the connection with the region and the people who live there have always played a central role at Feneberg," says Hannes Feneberg, who together with his brother Christof is the third generation to run the company as managing directors. "Regional production, close partnerships with farmers, animal welfare and environmental protection have been the cornerstones that characterise the production of our meat and sausage products for many years. With this in mind, it was important for us to also evolve in the packaging of these high-quality products and choose a variant that continues the sustainability criteria in production."
Switching to flow-pack packaging was a big step for the company, as the butchery in Kempten produces a total of 20 tonnes of minced meat and minced meat products such as burger patties or cevapcici per week. The main thing: "The new packaging has been very well received. We have obviously hit the nerve of our customers, who want more sustainability in their shopping," Hannes Feneberg concludes positively.
35.7 tonnes less plastic in circulation
At 60 to 65 microns, the flow pack is up to ten times thinner than conventional MAP trays, which are typically 450 to 650 microns thick. In addition, the flow-wrap bag is significantly lighter than the tray: Instead of tare weights of 13.58 to 24.98 grams for tray packaging, the film solutions weigh between 4.00 and 4.94 grams, depending on the size. As a result, Feneberg saves at least 70 percent plastic per package, at peak times even more than 80 percent. Calculated over the year, that is 35.7 tonnes less plastic that is put into circulation.
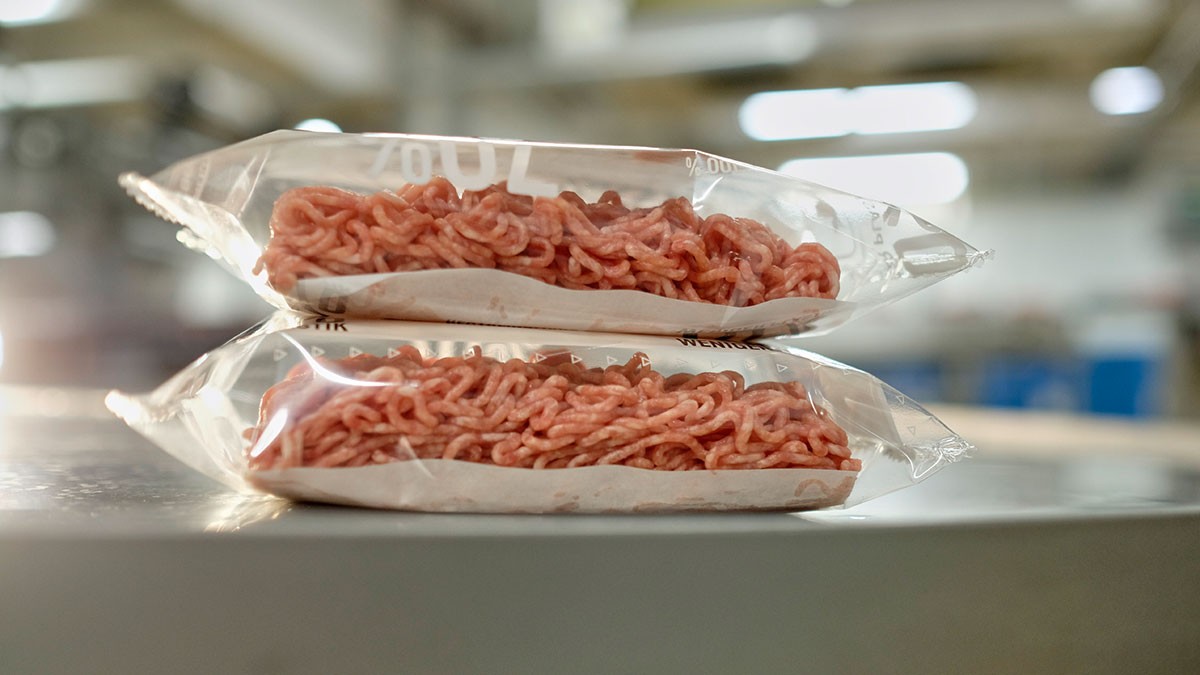
Stackable without crushing the minced meat: The flow pack with a modified atmosphere replaces the technical properties of a MAP tray 1:1. (Photo: © Ingo Jensen/Ulma)
Completely recyclable
Another sustainability plus for the tubular bags: The Monoflowre multi-layer film used by the film manufacturer Schur Flexibles consists of the mono material polypropylene (PP) and can be recycled without residues. And the flow packs make it particularly easy for the end user: Open the packaging, take out the meat and the unwashed film can be put in the yellow sack (used in Germany for recycling) and fed into the recycling process. "This simple handling without further separation convinced us," explains Christan Gareiß, Head of Production Technology at Feneberg. "Many other concepts that save plastic require an intermediate step from the end user. Often, for example, you have to peel a film off the box, which experience shows is not always done. The packaging then ends up in the residual waste. That's the end of the line for recycling before it even gets started," Gareiß continues.
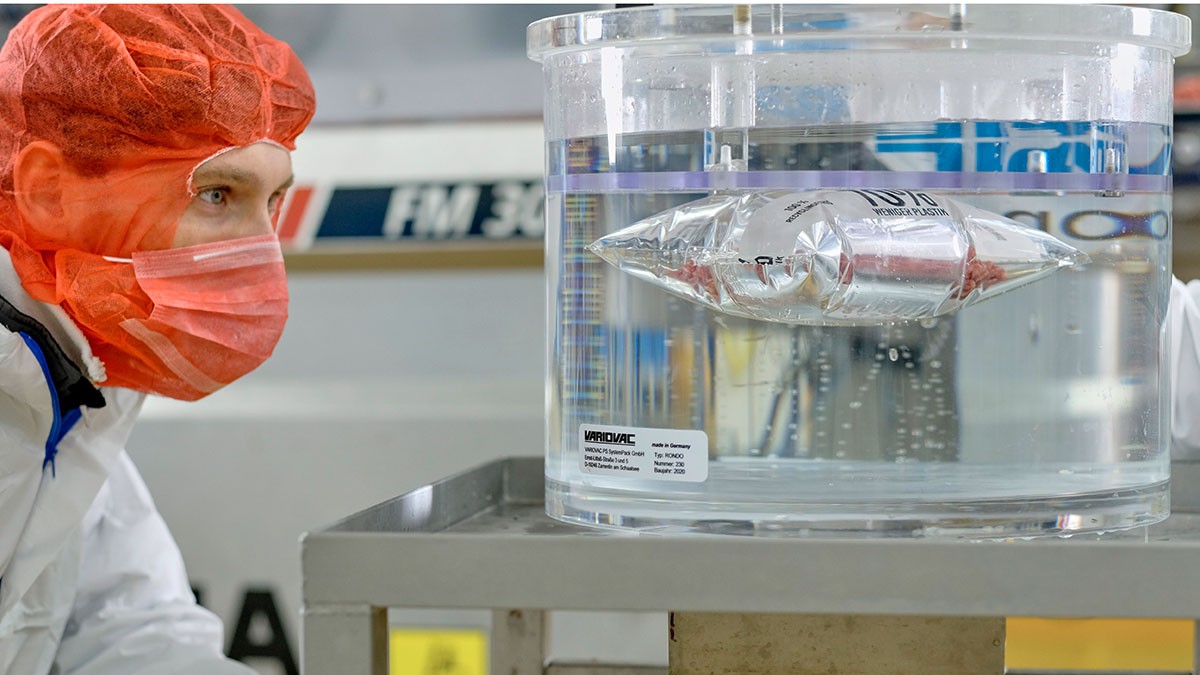
Christian Gareiß, head of production at Feneberg, randomly checks the leak-tightness of the flow-pack packaging. (Photo: © Ingo Jensen/Ulma)
Flow-wrap bag machine with new folding geometry
The self-service minced meat products at the production site of the Feneberg butchery in Kempten are packaged by the FM 300 flow-wrap bag machine from Ulma. For the recyclable PP film, the machine manufacturer has made some adaptations to its technology. "On the one hand, we have adapted the folding geometry, as the PP film buckles more quickly than other films. On the other hand, we have made changes to the longitudinal and transverse sealing to ensure the usual high sealing quality for the recycled film as well," explains Alexander Biechteler, Head of Technical Sales and Application Technology at Ulma Packaging.
Together with the new flow-wrap bag machine, Feneberg uses a total of seven Ulma machines in its production, in addition to packaging machines for minced meat, sausages and cold cuts, as well as systems for baked goods and ready meals. "For us it was clear that we would realise this important project together with Ulma. We have already been working together for ten years and know the machines very well," emphasises Gareiß from Feneberg. In the technical centre at Ulma in Memmingen, Germany, the two companies ran various product samples and tests and tested film types from several manufacturers.
Significantly lower logistics costs
Before the conversion to flow packs, one pallet of MAP trays was sufficient for 2,880 to 5,040 sales packs of minced meat and minced meat products. From the same transport volume with flow-pack material, Feneberg now generates between 64,8000 and 81,000 sales packages. Or to put it another way: "Instead of 100 truckloads of MAP trays, we now need just seven truckloads of film. That's a reduction of 93 percent. The savings in storage requirements are just as great," clarifies Gareiß.
The advantages on the economic side also have an effect on the ecological side. Due to the material savings and the reduced use of truck transport, the flow packs also significantly reduce CO2 emissions. The smaller packaging volume - compared to the MAP tray - also reduces the electricity consumption for storage, production and cooling of the products in the flow-wrap bag package.
Planned for the future
"The flow pack is the packaging of the future in the food industry. There's no way around it. We can't do without plastic completely, but we can reduce the amount used enormously. And after use, we can recycle the material completely - that's what a responsible approach to the environment looks like," emphasises Alexander Biechteler from Ulma. For the application technology manager, this offers the food and packaging industry enormous potential that can be quickly exploited.
"Because flow-pack packaging is a mature technology that doesn't have to be reinvented, it really can be implemented right away," adds Ulma Packaging Managing Director Thomas Blümel, thinking holistically: "For almost all products that are currently still packaged in MAP trays, the changeover to flow packs is feasible. So why wait?" That's how Feneberg sees it too. In the next step, the family business wants to convert the entire self-service meat range to packaging made of flow-wrap bags.