Hygienic Takeaway Guaranteed
No compromises when it comes to hygiene
Conveyor and process belts must ensure smooth operation around the clock. Synchronous movements and precise positioning play an increasingly important role given the high cycle rates of today's pick-and-place systems. It's always a matter of providing the goods produced at the right place and in the desired quantity at a specific time, while guaranteeing the highest quality. In this way, millions of food products are transported through production, to the packaging plant, to the cold store or to the loading station. At Anuga FoodTec, exhibitors will be showing belts in all widths and lengths and with a wide range of different flights, edges and other accessories. Equipped with smooth or textured surfaces, they transport a wide range of food gently and precisely - whether baked or deep-fried, delicatessen or frozen.
When it comes to ensuring safe transport in hygiene-sensitive areas in particular, the technology suppliers make no compromises. In addition to good cleaning properties, such as resistance to high temperatures, pressure, cleaning agents, disinfectants and mechanical loads, compliance with legal and industry-specific standards and regulations is the key requirement for conveyor technology that comes into direct contact with unpackaged food. The focus is on hygienic design. Easy cleanability of lines and components reduces the risk of contamination from product waste and deposits in gaps and recesses. The choice of conveyor and process belts plays just as important a role as the cleaning processes used in order to significantly extend the maintenance intervals of production systems.
Thorough cleaning of all components
For example, Habasit's monolithic and aramid-reinforced Cleandrive belts are suitable for both dry and wet applications. They are characterised by a smooth surface and have bars on the drive side which, together with special gearwheels, enable a positive drive and reliable transport performance. This means they combine the advantages of modular and fabric belts. The thermoplastic material used is resistant to chemicals such as cleaning agents and disinfectants and is compatible with the HyCLEAN Clean-In-Place system. This acts as an all-round belt cleaning system, cleaning inside and outside, both edges and the transport side. The belts are thoroughly cleaned and disinfected after up to seven rotations, reducing water consumption and the use of chemicals.
The HyCLEAN concept also includes patented gearwheels with a rounded design to ensure optimum cleanability. Exposing hard-to-reach areas on the back of the belt also enables all components to be cleaned thoroughly.
Completely sealed
Siegling Fullsan is the latest generation of hygienic conveyor belts from Forbo Movement Systems. These are homogeneous, thermoplastic polyurethane belts manufactured in accordance with FDA and EU regulations. What makes them special: The belts are completely sealed, which means they do not offer any points of attack for soiling from oil, grease, moisture and bacteria. They are suitable for use in particularly hygiene-critical applications. The high resistance allows regular sterilisation with UVC radiation. The belts are manufactured in a production width of up to two metres. This makes it possible to realise wider systems and increase the output quantity in food production. Some of the most important applications can be found in the meat/poultry and fish industries as well as in dairy products, which have high hygiene requirements.
The hygienic safety of the belts has been confirmed by the European Hygienic Engineering and Design Group (EHEDG). Both the fully homogeneous friction-locked polyurethane belt type FLT U30 GL/GL-NA-HACCP BL FDA and the aramid cord-reinforced type FLT+ U30 GL/GL-NA-HACCP BL FDA fulfil the strict guidelines of the EHEDG and have been evaluated and certified in accordance with EL CLASS I AUX.
The Prolink plastic modular belts, which are available in different designs for applications with packaged and unpackaged food, are also hygienic. The belts prove themselves both in straight-line transport and in curved positions. The version with a grid structure is particularly suitable where space is limited. The advantage: As very tight curve radii can be realised, the size and with it the footprint of the transport system can be significantly reduced.
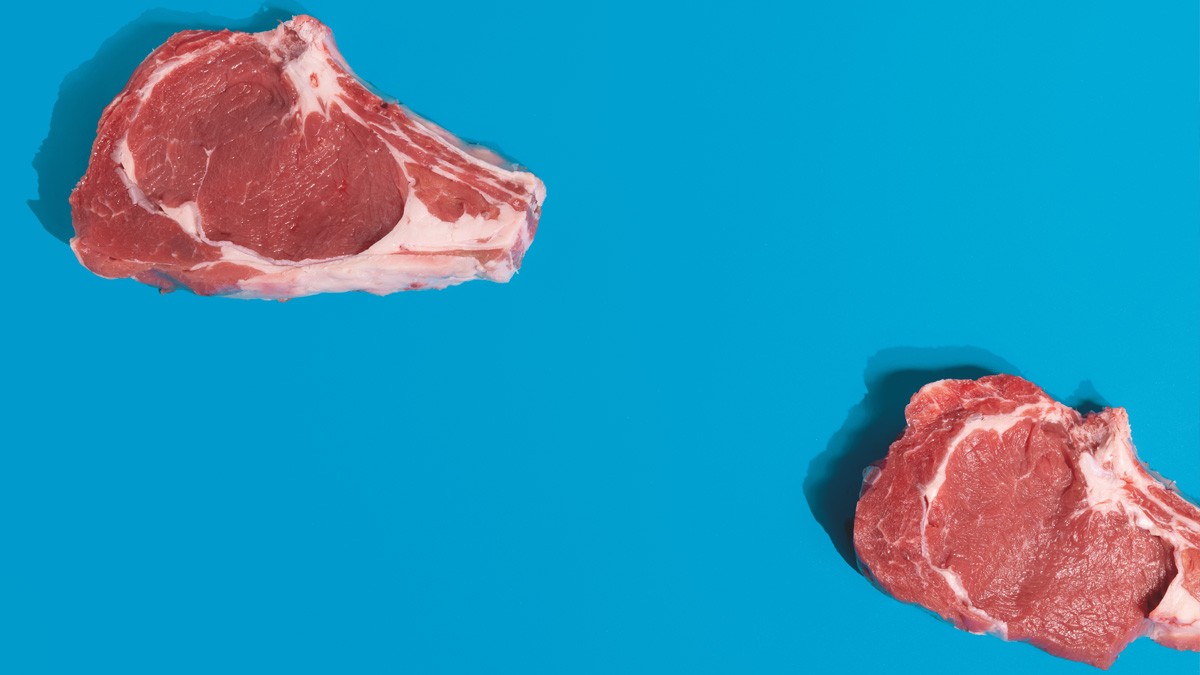
Siegling Fullsan products comply with current FDA and EU regulations and therefore provide the basis for maximum food safety in production and consistent support for the HACCP concept. Photo: Forbo Movement Systems
Oil-free drum motors
Belt operation via drum motors is recommended for driving conveyor systems in hygiene-sensitive environments. As the motor, gearbox and bearings are integrated into the drum, which is required in any case, the design offers advantages in terms of cleanability. In other designs, the motor and gearbox are usually designed as additional components. They have either fans, cooling fins or at least cooling surfaces that can create dead spaces and consequently nesting places for germs.
NGI is active in this sensitive area of food technology. The supplier's drum motors can be cleaned with water under high pressure. In addition, they do not require any oil, which rules out the possibility of contamination of the conveyed food. These are synchronous motors. They can run slow or fast with the same torque, making the overall design versatile, including fast starts and stops in packaging processes.
Efficient conveyor belt cleaning
Cleanliness, care and safety are three indispensable conditions in the production, packaging and distribution of food. Specialised conveyor and process belts support this requirement - especially if they are easy to clean. In order to reduce media consumption, companies specialising in cleaning equipment are also breaking new ground. The goal is to minimise time-consuming cleaning steps and reduce water consumption to an absolute minimum without neglecting the necessary hygiene. Frank will demonstrate this in Cologne with conveyor belt cleaners that can be customised for the respective location thanks to their modular design. The systems consist of a steam generator, an attachment and an industrial vacuum cleaner. The method enables a fully automated cleaning process. The belt is simultaneously cleaned and disinfected. The cleaned belt is then immediately dry and ready for use again. Another advantage: The use of steam leads to low water consumption. In addition, chemicals are generally not required for cleaning.