Greater Efficiency in Waste Heat Utilisation
Mr Hobusch, one of the food industry's strategies on the road to climate neutrality is to reduce emissions by increasing energy efficiency. What does this mean for Kaeser as a system provider in the field of compressed air generation and compressed air treatment?
Customised solutions for an energy-efficient compressed air supply have always been an essential part of development at Kaeser. Our products are continuously optimised to this end. The goal is to achieve even better energy efficiency with the highest possible availability and optimised overall cost-effectiveness for the customer.
Which technologies is Kaeser active with on the market?
The product portfolio includes screw and piston compressors with fluid-cooled or dry-compression. In addition, there are blowers and, depending on the degree of treatment required, refrigeration dryers, adsorption dryers, activated carbon adsorbers, filters for various quality levels, condensate drains and treatment devices, measurement technology and compressed-air management systems. We offer the right solution depending on the application and the required volumetric flow, the required pressure and the required compressed air-quality.
Operating costs, in particular energy costs, usually account for the lion's share. This is why compressor efficiency is so important when it comes to cutting electricity costs...
Yes, that's exactly how Kaeser sees it. As described above, the products are therefore constantly being adapted with a view to saving energy, for example by using drive motors of the currently highest efficiency class IE4 for fixed-speed systems. In addition, through improvements to the compressor blocks and the reduction of internal pressure losses through design measures. Another example is the use of electronic thermal management in the fluid-cooled screw compressors to optimally adapt the final compression temperature to the local cooling conditions, thereby reducing the required specific electrical power consumption.
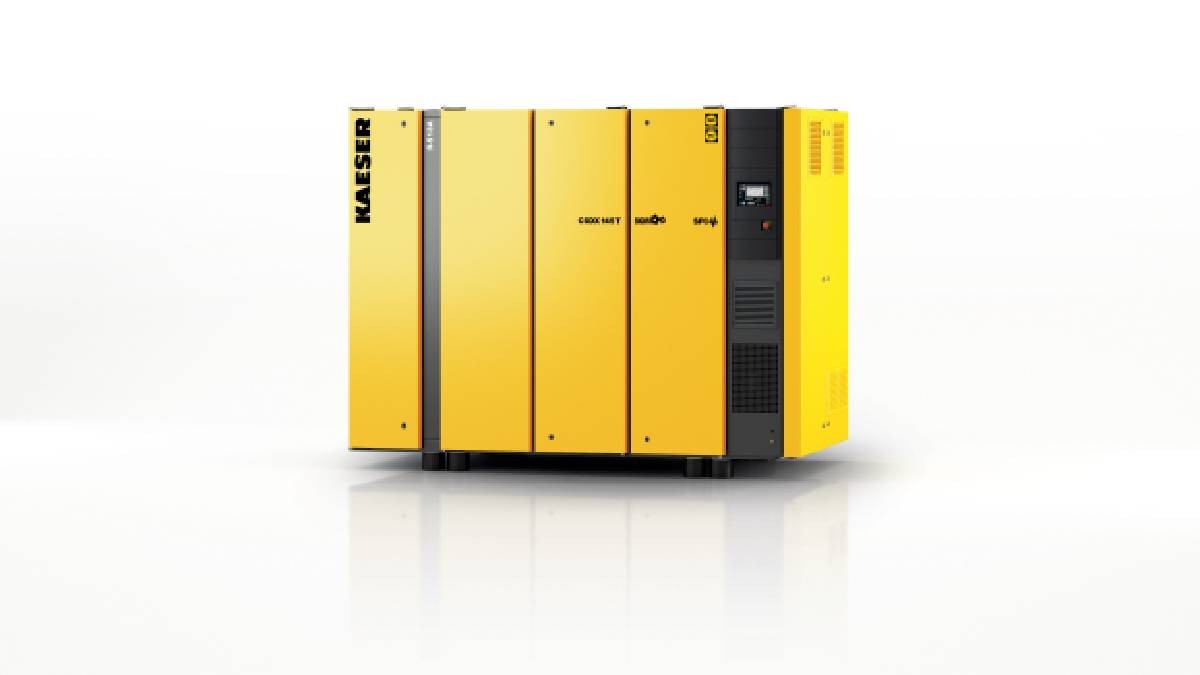
The CSDX screw compressor impresses with its high efficiency, reduced energy costs and sustainability. © Kaeser Kompressoren
Are there any other ways to reduce energy consumption?
Yes, via the control system. Energy can be saved both through internal compressor control and through a higher-level control system with a compressed-air management system and a consumption-based simulation-based optimisation process. Using the knowledge it has "learned" about the system and system behaviour, it can select the appropriate system configuration and determine the most efficient switching actions in advance.
Last but not least, it is advisable to recover the waste heat generated. What are the advantages for operators?
No less than 100 percent of the drive energy supplied to a compressor is converted into heat. Up to 96 percent of this can be recovered for secondary use. For operators, this means that they can significantly reduce energy costs and at the same time reduce their company's CO2 emissions as they use energy more efficiently.
What options are available for heat recovery?
The easiest way to do this is with an air-cooled compressor. For example, by using the waste heat to heat a neighbouring hall via an exhaust air duct. The air-cooled screw compressors are equipped with efficient and powerful fans with high pressure, which is why in many cases no additional exhaust fan is required. Other possible applications include drying processes, door curtain systems or the preheating of burner air.
What about heating service or process water?
Of course, the compressor waste heat can also be fed into existing hot-water heating systems and domestic hot water systems. The most cost-effective way to do this is with a plate heat exchanger. The waste heat from an air-cooled compressor can be used in the fluid circuit to generate hot heating and process water at temperatures of up to 70 degrees Celsius, or even higher if required. Up to 76 percent of the electrical power supplied is recovered as heat.
What are the typical processes in the food industry that generate waste heat, which is often dissipated unused?
In addition to the waste heat from compressors, as described above, large amounts of waste heat are released in the food industry during cooking, pasteurisation, baking, cooling and freezing. Depending on the technical solution, the waste heat can be utilised as exhaust air or in the form of hot water, as with compressors. For example, this is possible for hall ventilation and heating, including in production processes, or, in the case of large quantities, for the supply of district heating.
Are there any sectors that are particularly affected?
This may be the case in large breweries, dairies, bakeries or meat-processing plants, whereby the temperature level of the waste heat depends on the respective process.
From the beginning of 2025, the Energy Efficiency Act (EnEfG) requires companies to submit information relating to direct waste heat to the German Federal Centre for Energy Efficiency for the first time ...
Yes, that's right. The goal is to reduce final energy consumption by 26.5 percent by 2030 compared to 2008. The German federal government, federal states and companies are obliged to take targeted measures. Companies must avoid waste heat as far as possible by using modern technology. If waste heat is generated, it is to be reused through energy-saving measures wherever possible and reasonable.
The new EnEfG platform was also introduced ...
Companies must report information on the amount of waste heat and maximum output, temporal availability, control options and the average temperature level to the German Federal Office of Energy Efficiency by 31 March each year and update this information in the event of changes. The Federal Agency makes the reported information (under protection of business and trade secrets) clearly available on the public EnEfG platform for waste heat.
According to the new guidelines, it is no longer only important how big a company is, but also how much energy it consumes. So who is affected and what needs to be reported?
The Energy Efficiency Act applies to companies with an average total annual energy consumption of more than 2.5 gigawatt hours per year over the last three completed calendar years. A distinction is made here between consumption of over 7.5 gigawatt hours per year and consumption of over 2.5 gigawatt hours per year. Consumption is calculated for the overall structure of a company; if there are different operating sites or subsidiaries, the energy consumption is totalled.
In order to determine consumption, companies must continuously monitor their total energy consumption ...
Companies that do not operate an energy management system and have an energy consumption of more than 2.5 gigawatt hours per year are obliged to carry out and publish an energy audit at least every four years. Companies with a final energy consumption of more than 7.5 gigawatt hours per year must introduce an energy or environmental management system in addition to the measures already mentioned. The deadlines are regulated in the EnEfG.
Are there any exceptions to the reporting obligation?
No notification is required for installations that generate less than 200 megawatt hours of waste heat per year. Systems that are available for less than 1,500 operating hours per year or that have an annual average waste heat temperature of less than 25 degrees Celsius are also exempt. Locations at which the sum of the waste heat quantities of all waste heat potentials is less than 800 megawatt hours per year are also excluded from the reporting obligation.
Food companies with a consumption above certain limits are therefore faced with new requirements. What needs to be considered in advance when planning heat recovery?
The right heat sinks must be found on an individual basis. This means that the amount of heat available and the temperature level must be matched to the actual heat requirement. Depending on where and when how much heat is generated, it is possible to determine which applications can be supported or supplied. A consumption analysis can provide valuable information in the area of compressed-air supply.
How does Kaeser help with this?
In addition to the corresponding compressor technologies and services, we provide support in planning and analysing the compressed air requirements, creating piping and instrument flow diagrams for the compressed air station as well as installation drawings with piping and ventilation technology.