From laboratory scale to industrial production
Transforming ideas into reproducible processes
Alternative proteins can make an important contribution to securing the food supply for a growing population with fewer resources – “and thereby make our food system more sustainable and viable,” says Stefan Klebert, CEO of the GEA Group. In order to scale up developments in this sector on an industrial footing, the machine and plant manufacturer presented its mobile test centre at Anuga FoodTec 2022. As a fully-equipped, individually configurable process line, this modular fermenter and bioreactor platform can be used on a pilot scale for cultivating various cell types as well as for fermentation.
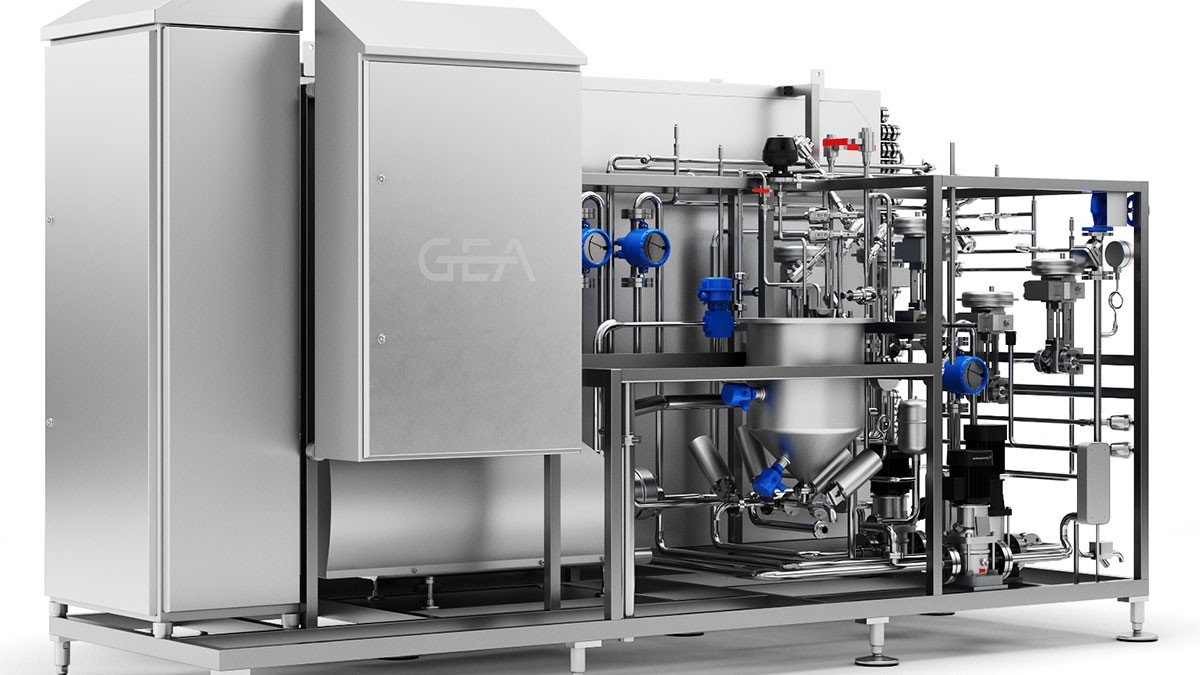
As part of the mobile test centre, the GEA UHT pilot plant is a flexible, highly-automated system for the indirect thermal treatment of liquid products such as fermentation solutions or dairy products. (Photo: © GEA)
For everyone entering new food terrain
So far, the leap from testing innovative foods in the laboratory to validating processes at an industrial level has necessitated significant investment in demonstration plants without any guarantee of success.
With its mobile test centre (MTC), GEA is aiming to achieve a new kind of proof of concept for cellular agriculture. The ingenious part is that customers do not have to invest in a complete pilot plant to support scaling up to commercial cell-based production. Instead, they can rent or buy the MTC or use it at a GEA branch, thereby enabling the growth and behaviour of cell cultures and microorganisms as well as fermentation processes to be studied, recipes to be modified, growth media and ingredients to be varied and process parameters that influence the yield and reproducibility to be influenced.
Fully equipped with eight technologies
The MTC offers the option of testing production with the aid of cell cultures and microbial fermentation using bioreactors/fermentation tanks on a pilot scale from 50 to 500 litres and complete process lines. It consists of eight technologies that comply with the food regulations, including GEA’s multifunctional fermenters or bioreactors as well as plants for mixing, heat treatment, homogenisation, separation and filtering. The system offers scope for changing the sequence of the various stages and for adding or repeating process steps in order to test cultivation and fermentation strategies as well as product recovery.