Faster and Better with AI
Usually, the contents of the sacks of lightweight packaging are roughly pre-sorted by size using machines and magnetic tinplate containers are separated out. Then batteries and other items incorrectly disposed of are removed from the contents by hand on the conveyor belts. Following this, a near-infrared (NIR) scanner usually detects the flow of waste. Using reflected light, the sensor can recognise different types of plastic, such as polypropylene, polyethylene or polyethylene terephthalate, thereby enabling them to be sorted.
In practice, however, problems arise time and again. For example, NIR technology cannot detect black plastics. Packaging with brightly printed stretch films or PE sleeves that are wrapped tightly around the product can also cause difficulties. Likewise, yoghurt pots with paper sleeves may be incorrectly categorised as paper waste instead of polystyrene packaging. Added to this are packages that have not been completely separated – for example, margarine tubs with bits of the aluminium lid still on them – or products that have been severely crushed. The consequence: They are incorrectly sorted and ultimately end up in landfills or incinerators. It is not uncommon for waste management companies to resort to manual re-sorting for this reason. This is very tiring work for the staff, and it significantly increases costs and slows down the process for the company. Otherwise, used plastics that could be reused or at least downcycled are actually lost.
Innovative sensor unit
In contrast, the focus at WeSort.AI is on an AI sensor unit consisting of optical systems such as NIR spectroscopy and digital cameras. The compact, box-shaped module is usually mounted at a distance of about one metre above the conveyor belt with the packaging waste: There, the system records a continuous video of the flow of waste. Image information is analysed in real time using artificial intelligence. In order to be able to determine what type of waste it is, the AI is trained with millions of data and images of commercially available food and non-food packaging. The computationally intensive task is made possible by WeSort.AI being able to use Microsoft data centres for this purpose.
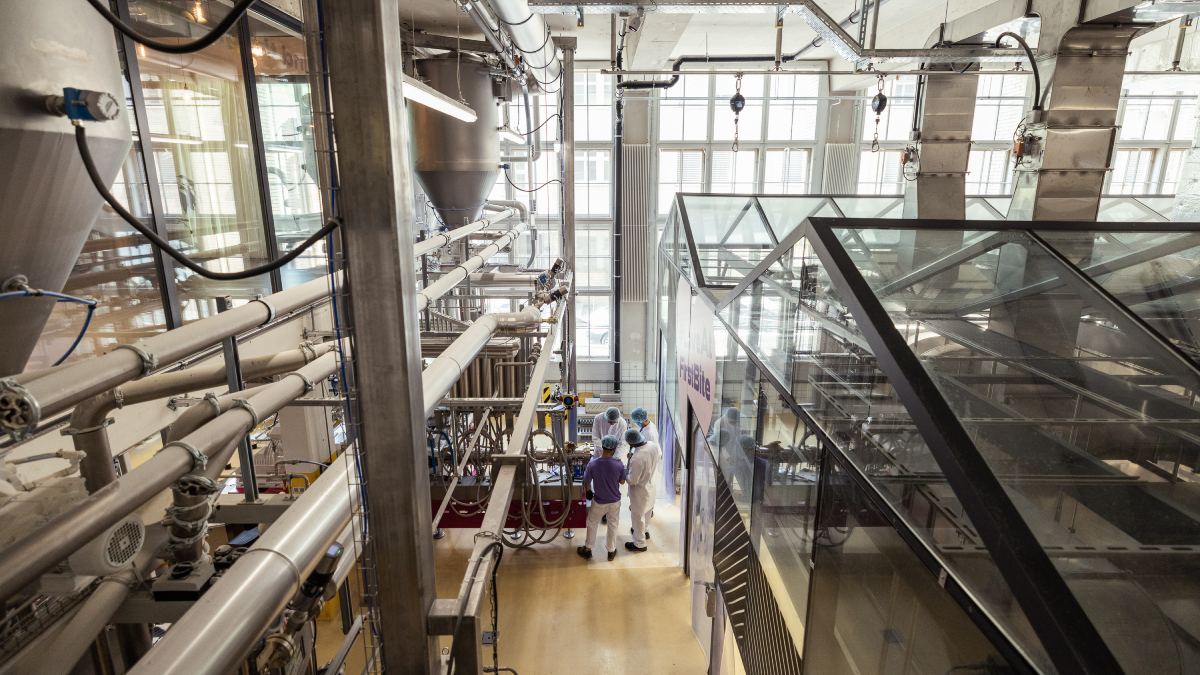
©WeSort.AI
Separation of single-material types at conveying speeds of two to four metres per second
By comparing the recorded sensor data with the collected information, the packaging is recognised as a whole, for example as a can, cup or bag. What's more, these items can also be identified as food packaging or other types of packaging. According to the company, which was founded in 2021, it is even possible to assign the data to specific brand-name products. This point is relevant in that only used plastic originally used for food packaging may continue to be recycled into food packaging in the future.
Continuous improvement
In the connected sorting chamber, nozzles are attached directly to the conveyor belts. These nozzles then use air pressure to blow each individual piece of waste into the correct material channel. The size and weight of the items are not important. Reinforcement learning is designed to further improve sorting accuracy. For this reason, the material channels are equipped with monitoring cameras that constantly optimise the AI object recognition algorithm with their feedback signal. WeSort.AI emphasises that a sorting accuracy of over 90 percent is already being achieved.
System users can keep an eye on all waste flows in live monitoring via the sensor unit, which serves as a central interface and displays a graphical representation of the process on a dashboard. Should risks or faults occur, warning messages will immediately provide information about them.
Modular and flexible
As Nathanael Laier, who founded the company together with his brother Johannes Laier, explains, the innovative system is mostly used for re-sorting. However, it could also be used for pre-sorting, for example to separate out hazardous materials such as batteries and scrap metal. The system could also be used in the waste paper sector to distinguish between cardboard and paper with and without printing inks.
WeSort.AI offers both complete systems consisting of sensor modules, sorting units and AI technology, as well as individual modules, depending on the respective requirements. Interested parties are welcome to see the technology in action. There are opportunities to do so at various events, or at the company's Würzburg technical centre, where twelve employees now work.
Contact data
WeSort.AI GmbH
Leighton Street 3
97074 Würzburg
Tel: +49 931 73047390
E-Mail:
contact-wesort.ai
Web:
https://www.wesort.ai/