Efficient, Sustainable Heat Supply
One of the main advantages of heat pumps is that they can work highly efficiently. The following applies here: The lower the temperature differential, i.e. the temperature difference between the heat source and the required flow temperature (heat sink), the higher the efficiency. If the temperature difference is 20 Kelvin, for example, the heat pumps achieve a COP (coefficient of performance) between five and six. This means that they generate five to six kilowatt hours of thermal energy from one kilowatt hour of electrical energy. This is usually sufficient, for example, to preheat fresh water with warm wastewater or warm exhaust air from cleaning. At a difference of 40 Kelvin, the COP drops to four or five.
The efficiency of a heat pump can be increased even further if it is used to generate both heat and cooling. Because it always produces both: Cold occurs where heat is removed, i.e. at the heat source. As heat and cold are almost always required in food processing, heat pumps are particularly suitable for this purpose. Companies can not only save or completely replace gas or oil for heat generation, but also electricity for re-cooling or compression cooling. However, a prerequisite for this dual use is a certain spatial proximity of the cooling and heating demand.
Major difference between conventional heating and heat pump
There is a fundamental difference between conventional heating systems and heat pumps: The former is centralized and therefore designed for the highest temperature required. A heat pump, on the other hand, is usually used decentrally. This means that the temperature required for the respective process is decisive. For example, a conventional heat pump that generates a flow temperature of up to 80 °C can be used for smoking or scalding. For sterilization processes, however, a minimum of 100 °C is required. High-temperature heat pumps (HTHPs), which can reach temperatures of up to 140°C, are suitable for this purpose.
Yet the use of a heat pump often makes sense even if it does not provide the required flow temperature. Typically, the heat pump is then used for preheating. However, it is also possible to cover preheating with fossil fuels and then use the heat pump to reach the target temperature. This in itself reduces the amount of fossil fuels required, and consequently also CO2 emissions.
In addition, several heat pumps can be combined in a cascade connection. This makes it possible to achieve a higher temperature level and to switch the individual heat pumps on and off as needed. Thanks to this flexibility, this type of combination can also be more sensible than a single more powerful heat pump
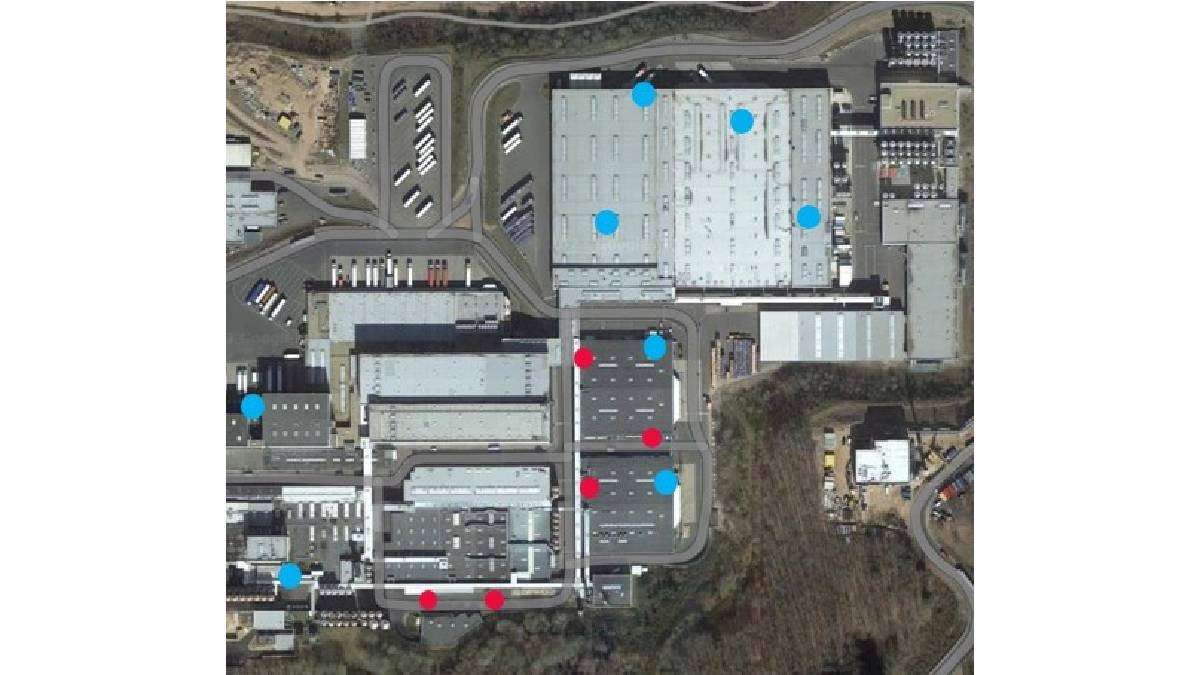
Potential heat sources (red) and heat sinks (blue) in the company. ©MVV Energie AG
Step by step to a sustainable heating concept
However, the use of a heat pump is not always practical or economically viable wherever it is theoretically possible. In order to arrive at a viable concept, the circumstances of the respective company must be considered in detail. The following approach has proven effective in the business customer unit of MVV Energie AG:
The first step is to identify the possible heat sources and sinks in the company (Fig. 1. Possible sources of heat include, for example, wastewater from the cleaning process or from process cooling (cooling water), exhaust air from drying and cooking processes, and flue gases.
The heat sink is the point in the process where the useful heat is coupled in. These are typically all processes that require hot water, such as cleaning or hot filling. With a high-temperature heat pump, drying, pasteurization and distillation processes, for example, are also possible.
The next step is to check which heat source and heat sink can be practically connected. Here, not only the distance must be taken into account, but also how much heat is available at which temperature level at the source and what the load profile looks like. In addition, the heat source and sink must also be accessible.
On the basis of these aspects, some heat sources or sinks are not suitable for use with a heat pump (Fig. 2). Those that remain can be prioritized according to their potential. If the potential is great, but the waste heat and heating requirements occur at different times, a buffer storage tank may be worthwhile.
It is often advisable to switch from steam to hot water where the process allows. This is because the heat pump's required system technology is simpler and therefore cheaper. Moreover, its COP, i.e. its efficiency, also increases. This type of conversion is possible wherever temperatures below 100°C are required, which were previously applied with steam, for example in pasteurization or in cleaning machines for reusable containers. However, to do this, the supply network must be converted from steam to hot water and the corresponding consumers must be equipped with larger heat exchangers.
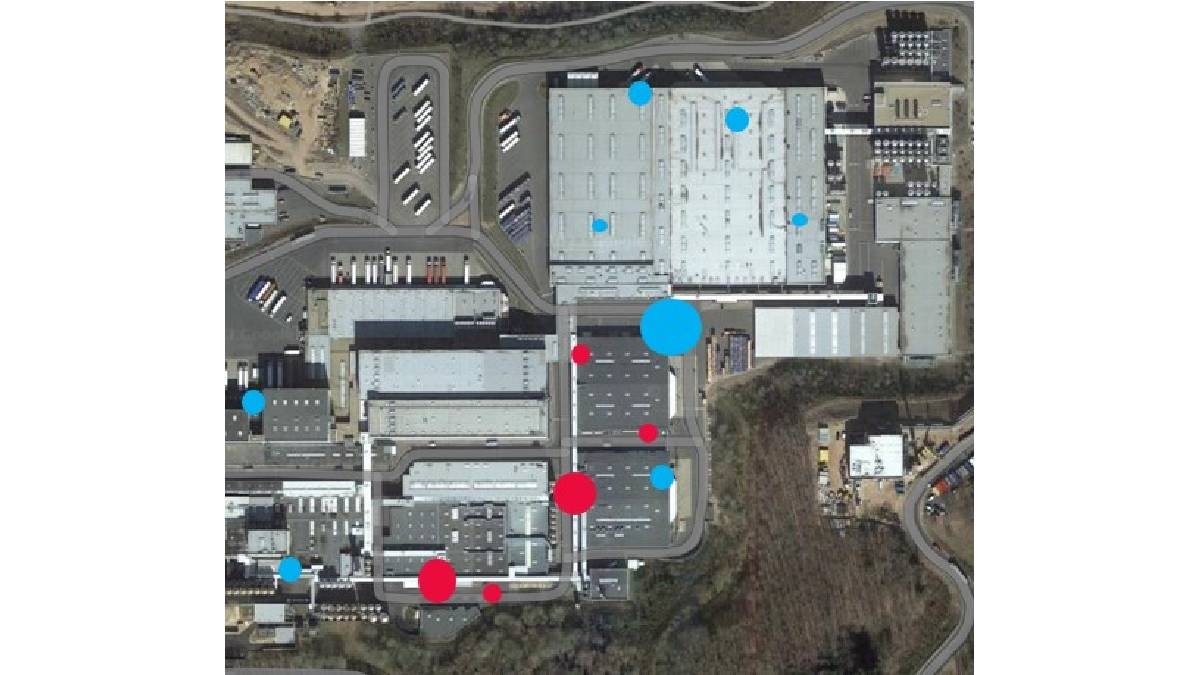
Actual usable heat sources and sinks with their potential (the size of the dot indicates the potential). ©MVV Energie AG
Profitability analysis
Generally speaking, heat pumps have a long service life and require little maintenance, which means that operating costs are usually lower than for conventional heating systems. A profitability analysis can determine whether the heat pump also makes economic sense in the specific application scenario. In addition to the heat pump type, the operating conditions and the costs for developing the heat source and heat sink must also be considered.
Because the heat pump is operated with electricity, the price of electricity also plays a role. Thanks to the 7,000-hour rule, energy-intensive companies may even be able to benefit financially from the increase in electricity consumption. If they exceed 7,000 full-load hours
per year, their grid fee is reduced to 20 percent, to 15 percent from 7,500 hours, and to as little as ten percent from 8,000 hours.
As the heat pump usually replaces natural gas, the gas price should also be considered as a comparative energy source.
Subsidies for heat pumps
The investment costs for a heat pump are currently still usually higher than those for a gas boiler with the same thermal output. To compensate for this difference, extensive subsidies are currently available. For example, the use of a heat pump to utilize waste heat from production is being promoted as part of the “Energy and Resource Efficiency in the Economy” (EEW) funding program, Module 4. The costs for the heat pump, as well as for heat storage and additional costs, are eligible. The subsidies available to small companies cover up to 45 percent of the extra investment costs. For medium-sized companies, the figure is up to 35 percent, and for large companies, up to 25 percent. Alternatively, companies can also choose to have their total costs subsidized, in which case the rates are 20 (small companies), 15 (medium-sized companies) and 10 percent (large companies).
Heat pumps for space heating are covered by the German federal funding for energy-efficient buildings (BEG). Here, the funding is scaled according to the net floor space affected by the measure.
However, the decisive factor is that the use of a heat pump should help to sustainably secure the competitiveness of food processing companies by reducing the demand for fossil fuels. If the heat pump is operated with electricity from renewable sources, it even operates in a climate-neutral manner and helps the company to achieve its climate targets.
Further information on the topic: https://hubs.li/Q02Tp-bk0
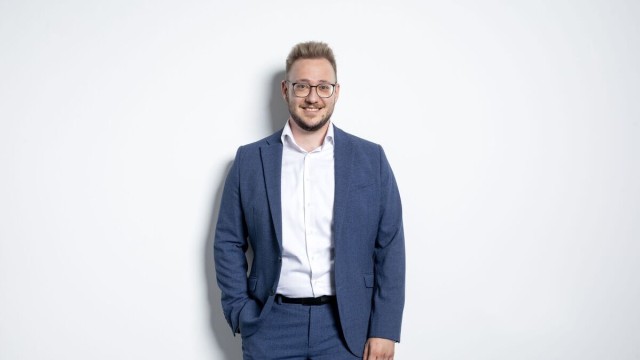
Lars Manja, Key Account Manager , MVV Energie AG. ©MVV Energie A
For additional information, go to:
Lars Manja
Business Customer Sales, Key Account Manager
MVV Enamic GmbH
https://partner.mvv.de