Convincing eco-balance
Solid Data
In terms of sustainability, the potential savings identified in SÜDPACK’s internal evaluations were substantiated by the LCA with hard facts. The results come as no surprise, as printing processes typically involve high material and energy consumption due to color changes, cleaning procedures, and proofs.
The certified LCA clearly demonstrates the advantages of SPQ over the conventional flexo print process for various print carriers. “From an environmental stand-point, all viable printing processes should be transitioned to this new technology. Only orders requiring spot colors still make the conventional flexo print process a viable option,” says Carolin Grimbacher, Managing Partner at SÜDPACK.
SÜDPACK offers its customers a range of printing processes for package printing. In the latest LCA study, the potential environmental impact of the SPQ printing process was compared with the conventional flexo print method for OPP and PET substrate films.
The functional unit (FU) used for comparison was 1 m² of printed OPP or PET substrate film, without the application of spot colors. Various scenarios were calculated for both the SPQ and flexo print process, including the use of 20 μm OPP film and 12 μm PET film as the print carrier. Another scenario analyzed the impact of different energy sources on production at SÜDPACK. For all scenarios, key im-pact categories such as climate change, fossil raw material consumption, and the effects of photochemical ozone formation on human health were evaluated.
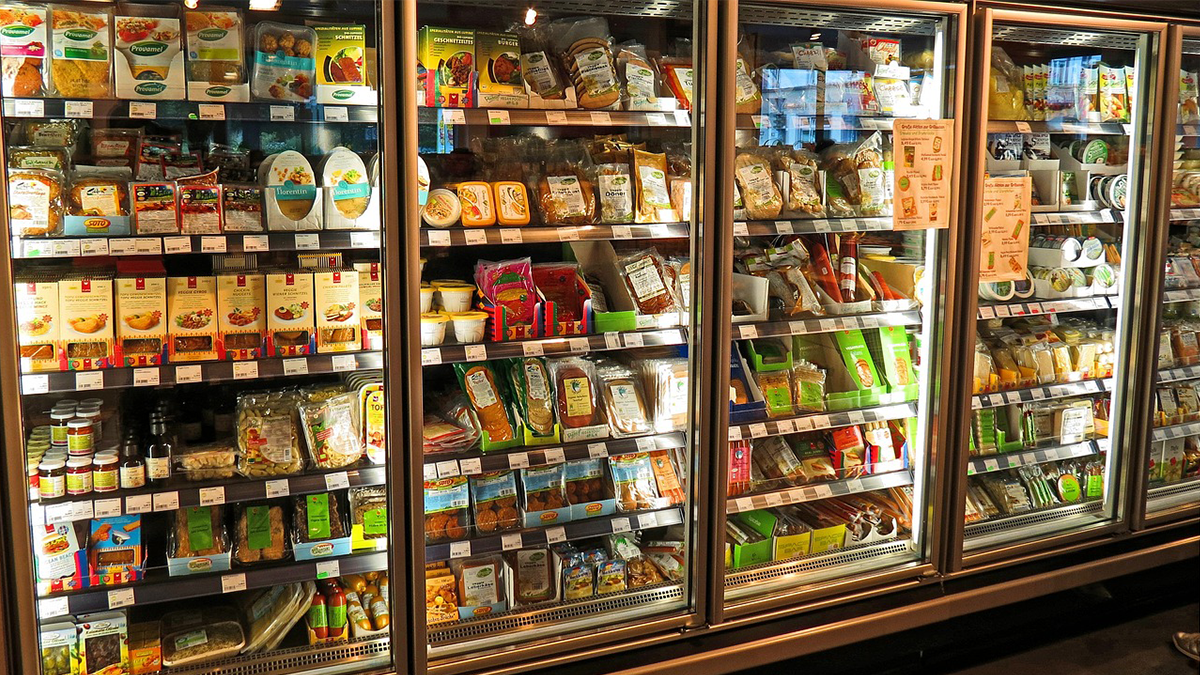
SÜDPACK offers its customers a range of printing processes for package printing. In the latest LCA study, the potential environmental impact of the SPQ printing process was compared with the conventional flexo print method for OPP and PET substrate films. ©Pixabay
Clear Results
The study found that switching to SPQ printing technology can reduce CO2 emissions by 18% for both PP and PET print carriers. Even in the best-case scenario for the flexo print process (using green electricity), its carbon footprint was still 11% larger than the worst-case scenario for SPQ (using the grid mix). From an environ-mental perspective, the recommendation is clear: Wherever possible, print products should be transitioned to SPQ, with the conventional flexo print process re-served only for orders requiring spot colors that cannot be reproduced with SPQ.
About SÜDPACK
SÜDPACK is a leading manufacturer of high-performance films and packaging solutions for the food, non-food, and medical goods industries, as well as customer-specific compounds for technically demanding applications.
The family business, which was founded by Alfred Remmele in 1964, is headquartered in Ochsenhausen. The production sites in Germany, France, Poland, Switzerland, the Netherlands and the USA are equipped with the latest plant technology and manufacture to the highest standards, including the capacity to operate under clean room conditions. The global sales and service network ensures a high degree of proximity to the customer and comprehensive technical support in more than 70 countries.
With its innovative Development and Application Center at its headquarters in Ochsenhausen, SÜDPACK offers its customers an optimal platform for developing tailor-made solutions and performing application tests.
SÜDPACK is committed to sustainable development and fulfills its responsibility as an employer and towards society, the environment and its customers. For its sustainable product developments and consistent commitment to a functioning circular economy in the plastics industry, SÜDPACK has received numerous awards.
Further information is available at www.suedpack.com