Automation is Key in the Low-Temperature Warehouse
Dematic is a leading global provider of warehouse automation and software solutions. As part of the KION Group, the company develops customised automation systems for the EMEA region at over ten locations in Europe. One of these is the KION Automation Center in Antwerp, Belgium.
KNAPP Systemintegration is part of the internationally operating KNAPP group and specialises in implementing solutions for food and empties logistics, meeting the specific requirements of the food industry with top quality. The solution portfolio includes innovative automation concepts for the stationary and online food trade.
In this article, Stijn Wouters, Sales Manager at Dematic, and Rudolf Hansl, Vice President of Food Retail Solutions at KNAPP Systemintegration, explain how innovative technologies increase efficiency in deep-freeze warehouses and which strategic measures companies should take.
Challenges in frozen food logistics
Deep-freeze warehouses with temperatures below -18°C present companies with particular challenges. Extreme cold puts a strain on machines, materials and work processes. Humidity control is essential for preventing ice formation, which can impair both the operational reliability and the efficiency of the technology.
"Standard machines often fail in extreme cold because they require special materials and lubricants," explains Stijn Wouters, Sales Manager at Dematic. What's more, protective clothing and regular breaks slow down work processes. Mechatronic components are also affected. "Deep-freeze temperatures place enormous pressure on storage technology. Specially developed toothed belts, cold-resistant lubricants and a controlled cool-down phase are essential for ensuring long-term functionality," adds Rudolf Hansl, Vice President of Food Retail Solutions at KNAPP Systemintegration. Only a combination of customised technology, precise process control and automation can sustainably optimise efficiency and operational reliability in deep-freeze warehouses.
Automation: Increased efficiency in deep-freeze warehouses
Modern warehousing technologies are crucial to reducing energy consumption, optimising costs and accelerating processes. Automated systems take over key tasks such as picking, palletising and warehouse management – even at temperatures as low as -28°C.
One example of this is the Evo Shuttle for all temperature zones from KNAPP. "The system optimises order picking and ensures better use of space and lower energy costs thanks to its multiple-depth storage," explains Hansl. Intelligent algorithms ensure optimal utilisation, while the compact design enables uniform cooling.
Dematic also relies on high-performance automation solutions that are adapted to the extreme conditions of deep-freeze warehouses. "Our solutions range from high-density pallet high-bay warehouses to fast goods-to-person systems such as the Multi-Shuttle," emphasises Wouters. A central role is played by the warehouse management software (WMS), which manages stocks in real time and optimises the flow of materials.
The use of robotics and AI in deep-freeze warehouses continues to increase. "Robots not only increase efficiency, but also reduce operating costs through more precise processes and optimised warehouse management," emphasises Hansl. At the same time, AI-supported systems improve inventory management and demand forecasting. "Machine learning algorithms ensure faster, more accurate order processing," adds Wouters.
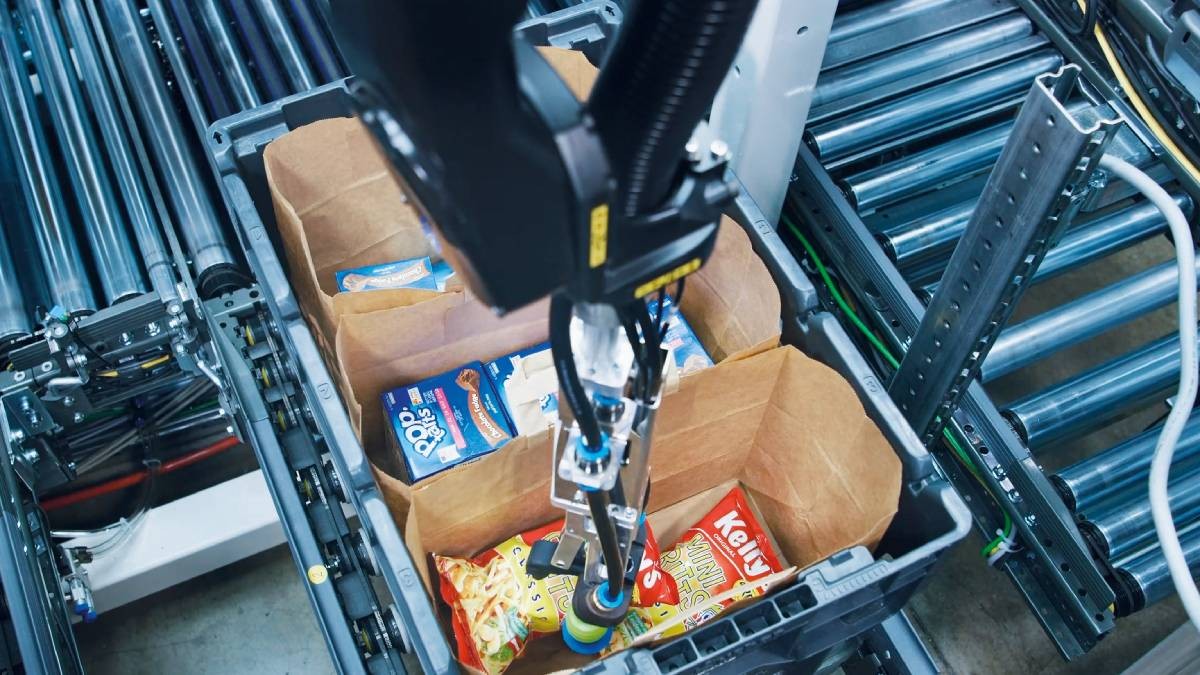
The Pick-it-Easy Robot from KNAPP is ideal for online grocery retailing, with optimal gripping technology and gentle article delivery. @ KNAPP Systemintegration GmbH
Examples of best practices
Automation offers great potential for savings with regard to energy, personnel and space utilisation. "Automated systems significantly reduce personnel costs, as robots can work around the clock without requiring breaks or protective clothing," explains Hansl. At the same time, cooling performance is improved and operating costs are reduced through a more efficient use of space. "High-density storage systems maximise available volume and reduce energy consumption through optimised cooling zones," adds Wouters.
One example of successful automation is the collaboration between Dematic and Agristo, a world leader in the production of frozen potato products. Six fully automated high-bay warehouses enable greater storage capacity in the same space, shorten order processing times and optimise energy efficiency. This is achieved by reducing the number of times doors need to be opened and improving temperature control.
KNAPP has also developed an innovative Central Fulfillment Center (CFC) with the grocery retailer Shufersal. The facility processes up to 7,800 orders daily and includes five temperature zones, including a deep-freeze warehouse at -24 C. "Thanks to intelligent algorithms running in the background, we achieve a picking performance of 600 units per hour and workstation," explains Hansl.
Conclusion: Efficiency and outlook
Automation is the key to optimising deep-freeze warehouses. "Automated processes increase performance, reduce costs and minimise the physical strain on employees," explains Hansl. Companies with high picking performance in particular benefit from efficient systems that enable shorter throughput times and higher storage capacity.
Sustainability also plays an increasingly important role. "Minimising unnecessary movements in the warehouse improves cooling performance and significantly reduces energy consumption," emphasises Wouters.
The boom in e-commerce is also placing new demands on frozen food logistics. "Smaller, highly automated warehouses near the city centre enable fast, efficient delivery. Optimised delivery time slots and intelligent refrigerated transport improve delivery logistics and increase customer satisfaction," emphasises Hansl. At the same time, AI-supported systems are gaining in importance. "They optimise storage strategies, improve demand forecasts and help companies to reduce costs," adds Wouters.
Those who adopt intelligent, sustainable automation at an early stage will secure long-term economic advantages and a stable market position. The experts agree that a gradual approach to automation is often the best way to exploit efficiency potential in a targeted manner.
If you have any questions, please contact:
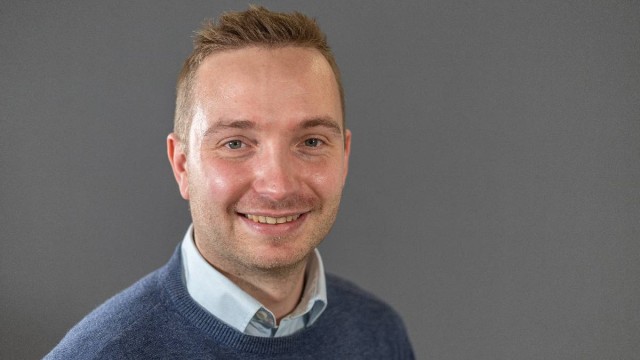
Stijn Wouters, Sales Manager, Dematic NV Antwerp. © Dematic NV, Antwerp
Stijn Wouters
Sales Manager
Dematic NV
B-2050 Antwerp
Belgium
E-Mail:
stijn.wouters@dematic.com
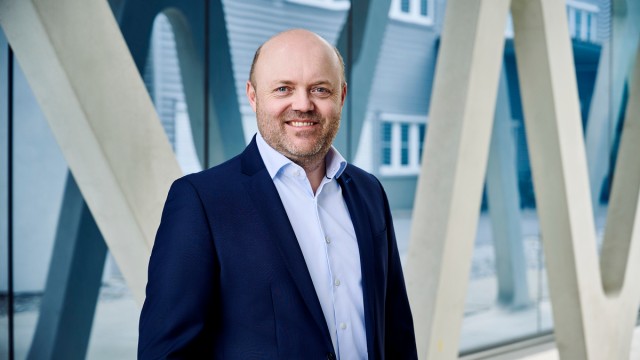
Rudolf Hansl, Vice President Food Retail Solutions & Member of the Management at KNAPP. © KNAPP Systemintegration GmbH
Rudolf Hansl
Vice President Food Retail Solutions &
Member of the Management
at KNAPP Systemintegration GmbH in Leoben, Austria.
E-Mail
ksi.sales@knapp.com