Automatic testing system
Heat exchanger integrity testing is essential for the safe and efficient operation of industrial systems and processes. Heat exchangers are used in a wide range of applications, including fluid processing, power generation, chemical processing, HVAC systems, and refrigeration. Manufacturers are all too aware that their pasteurizers, plate and tube heat exchangers are susceptible to cracks and other defects during their lifetime, which can cause severe contamination and ultimately lead to consumer health problems, reputational damage or costly product recalls.
HEIST – Non-destructive integrity testing
HEIST is an innovative and patented system designed for non-destructive integrity testing of heat exchangers. Unlike traditional methods that rely on regular testing (usually 1-4 times a year), daily testing is made possible before the start of production, so that cracks or defects in the heat exchanger plates are detected in time and the risk of product contamination is reduced. The system includes sensors, valves, and pumps that integrate seamlessly with existing equipment, and also enables an automated testing process for both plate heat exchangers (PHEs) and pasteurizers.
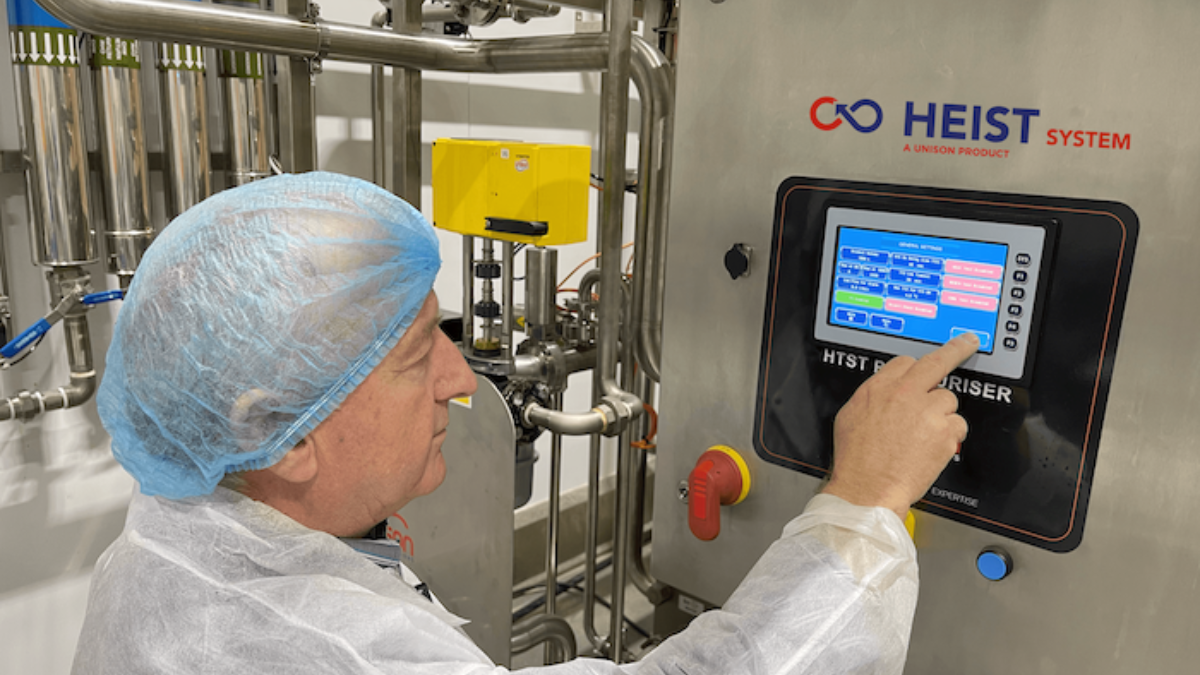
Unison Process Solutions has launched HEIST, an innovative, patented system that enables the non-destructive integrity testing of heat exchangers. ©Unison Process Solutions
Integrity certificates increase reliability
Additional tests, such as diversion valve tests and hold time checks, can be performed to ensure the overall integrity and efficiency of the heat exchanger system. While traditional methods require the heat exchanger to be dismantled, here a non-destructive testing approach is adopted that does not damage the equipment during the testing process, minimizes downtime and avoids equipment damage. The sensors and algorithms used work with high precision and can identify cracks and defects in heat exchangers up to a size of 50 μm. In addition, instant digital test results, so-called integrity certificates, are provided, eliminating the need for interpretation by the operator and increasing the reliability of the test process and also that of data integrity. Data can be easily accessed, shared, and analyzed, enabling informed decision-making and effective maintenance planning. There are further applications in sustainable resource management or the recovery of waste and by-products. For example, the sensors can measure milk residues or other products in the rinsing and cleaning water and determine approaches to reduce or eliminate waste. By-products can then be recovered and processed elsewhere if necessary.
Further information: www.unisonprocess.com