Automated Guided Vehicles
Mobile robotics on road to growth
From conveyor belts to industrial trucks, from high-bay warehouses to Scara robots and cobots - Anuga FoodTec 2024 has once again shown how food manufacturers are optimising and redesigning their movements within the plant. Whereas 20 years ago, simple, repetitive processes for warehouse automation were still the order of the day, today integrated and complete turnkey solutions are in demand. At the same time, the trend towards autonomous vehicles is continuing in intralogistics. One reason for this is that they can take on many transport tasks between incoming goods, production and the warehouse: More than half of all professional service robots worldwide are now used for this type of work. According to figures from the International Federation of Robotics (IFR), sales in this segment rose by 44 percent in 2022, with a good 86,000 units sold.
On the other hand, automated guided vehicles (AGVs) have become an essential component of flexible intralogistics. And that’s because the demand for skilled workers and labour in internal material flows is becoming increasingly noticeable. "The shortage of drivers and warehouse workers is a critical factor in global supply chain management," says Marina Bill, President of the International Federation of Robotics (IFR). A new generation of AI-supported transport systems is expected to help overcome these challenges. "Robot manufacturers combine their hardware with intelligent software to meet the specific automation needs of the warehousing and logistics industry. Autonomous mobile robots equipped with artificial intelligence open up an enormous number of new opportunities for this sector," says Bill.
Orientation in a dynamic environment
The use of AI is mainly aimed at dealing with variability and unpredictable situations. To enable the machines to support flexible and autonomous work processes in the food warehouse. Instead of programming, the software relies on an experience-based learning process - and on laser-assisted navigation systems. Additional infrastructure, such as guide rails or light reflectors, are not necessary for autonomous mobile robots (AMR). The vehicles scan their surroundings in all directions using laser sensors. SLAM navigation (Simultaneous Localisation and Mapping), which was further developed at the Fraunhofer IPA (Institute for Engineering and Automation), has established itself as the standard for free path planning. A LiDAR-based scanner scans a planar area several times a second. The distance data of the orientation points obtained in this way are compared with a map of the surrounding area stored in the system and enable the AMR to determine and adjust its position in real time.
Another method is Visual SLAM technology. Instead of a LiDAR scanner, it works with several cameras that enable the robot to perceive things stereoscopically. "In contrast to the two-dimensional SLAM method, points are not only captured on a plane, a 3D point cloud is generated. This opens up a previously unattainable accuracy range of less than one centimetre," explains Stefan Zernickel, Engineering and R&D Director for AMR at ABB Robotics. This enables vehicles to make intelligent decisions and distinguish between fixed and moving objects in dynamic environments where people are present. Equipped with image processing technology and AI, each mobile unit scans a specific part of the building. The fields of vision of all robots are combined to form a complete map so that the AMRs can also work in rapidly changing environments. The maps are continuously updated and shared across the fleet, enabling instant scalability without interrupting operations.
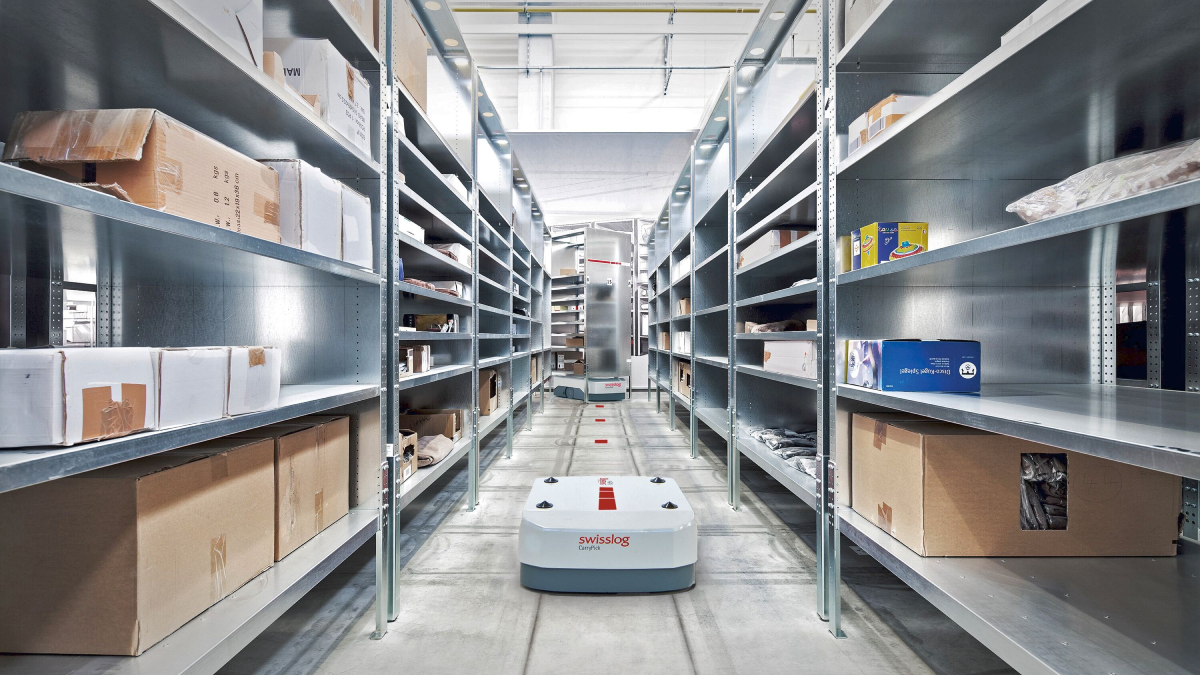
© KUKA
24-hour operation in sorting empties
It is this unrestricted mobility that opens up completely new areas of application for food and beverage producers. Almost every type of industrial truck known in manual operation can be used in an automated guided vehicle (AGV) system. These include autonomous tractors, high lift trucks, counterbalanced high lift trucks, reach trucks and narrow-aisle trucks. With six automated guided vehicles from the modular "Vario Move" series, ek robotics recently realised a corresponding intralogistics solution for a large family-run brewery. The new automation process revolutionises the previously manual forklift transport of unsorted and sorted empties. The transport solution comprises six high-performance transport robots from the modular Vario Move series. Equipped with a special combination of two load handling attachments, they take over the transport between numerous conveyor systems, robot cells and other transfer stations in 24-hour operation. The AGVs also serve two block storage areas, where they store and retrieve stacks of pallets and transport new glass provided there to the transfer stations of the conveyor systems.
"The special feature of the vehicles is the interaction between the equipment clamp and the height-adjustable fork pair, which enables separate distribution of empties and pallets," says Guido Wendel, the responsible sales engineer at ek robotics. Before a transport robot reaches one of the nine transfer stations of the robot cell, the empties are fixed with the clamp, the pallet underneath is lowered with the fork and thereby separated from the empties crates. In the next step, the empties are placed on the conveyor system without the pallet and the empty pallet is then transferred to another station. After the empties system has sorted the products, the automated guided vehicles pick up the empties again, return the crates to an empty pallet and complete the cycle by delivering their load to the filling system.
Maximum freedom without safety fences
This example illustrates that the boundaries between automated guided vehicles (AGVs) and AMRs are becoming increasingly blurred. "In recent years, technology in the field of automated guided vehicles has continued to develop in the direction of autonomous mobile robots," confirms Jan Drömer, CIO of ek robotics GmbH from Hamburg. Background to this statement: Typically, an AGV is a complete system consisting of a control system, data communication, charging stations and, if necessary, other devices for determining the location. The associated automated guided vehicles are usually track-bound, which means that companies must carefully consider the optimum route in the warehouse before integration. Once the route network has been planned, changes are accompanied by adaptation and repeated optimisation efforts.
Just like AGVs, AMRs take on physically demanding transport tasks and, thanks to their extensive safety technology, can share routes with employees and conventional industrial trucks. "In this case, the vehicles stop safely and also emit an acoustic and visual warning. Only when the path is clear again do they continue the transport," explains Felix Tschorn, AGV Solutions Project Manager at KUKA. The KMP 600-S diffDrive from KUKA is an example of this type. At up to two metres per second, the mobile platform is not only fast, but also meets the most stringent safety requirements thanks to laser scanners and 3D object recognition. Despite a load capacity of 600 kilograms, it allows maximum freedom of movement for employees as it does not require safety fences. While AGVs were developed specifically for material transport in industry, AMRs can also be used in other areas. For example, once a cobot has been installed, the mobile platforms can take over pick-and-place applications or palletising tasks. Whether for narrow-aisle warehouses, mobile shelving systems or assembly lines: "Automated guided vehicles are a key technology and a significant motor for efficiency in innovative processes. And they enable available skilled labour to be deployed more efficiently," emphasises Ronald Kretschmer, Chief Sales Officer at ek robotics. The expert is certain: The general trend towards automation in intralogistics will continue to accelerate.