Aseptic Processing
"When planning a corresponding processing plant, food companies and plant planners usually focus first on tanks, separators and other large components. However, smaller components such as valves and pumps should also be included in the considerations as early as possible, as they have a major influence on product and process reliability." This is emphasised by Pascal Bär, Senior Director Product Management for Aseptic Valve Technology at GEA.
GEA also offers a comprehensive range of aseptic valves under the Aseptomag® brand. The range includes valves for shutting off pipelines, for switching and filling, for regulating and sampling as well as double chamber valves for the mix-proof separation of intersecting product lines. In contrast to classic hygienic valves, aseptic valves are characterised by a hermetic seal between the product-carrying interior and the environment. These are generally required in particular after thermal preservation of sensitive products. From that point onwards, contamination from outside entering the sterile process area must be reliably prevented.
There is a choice of stainless steel metal bellows, PTFE bellows and rod or stem diaphragms. "Each of these technologies can be used in various industries and applications. The combination of a material and its special shape characterises differing protective properties for the processed substances. Which technology is ultimately used in a system depends on the product and process requirements," says Bär.
Metal bellows valves pay off
Aseptic valves with metal bellows are characterised by their accordion-like shape and thin walls, which make them both stable and flexible. Introduced decades ago, they are still regarded as the highest class of aseptic valves and are, for example, virtually standard for baby food. One reason for this is that stainless steel is a proven inert material. The other advantage is their inseparable welded connection, which is not possible with other types of hermetic sealing. This means that the so-called "lift effect" and the associated carry-over within the product-carrying area can be mechanically ruled out. The movement of the valve stem from the non-sterile outside world into the product-carrying space is known as the lift effect, which can bring contaminants or germs from outside into contact with the food. Carry-over can occur due to detachable connections between two or more parts, especially if the materials of the individual components react differently to the prevailing process conditions.
In this context, the expert adds that there are also areas for which classic hygienic valves or valves with rod diaphragms are ideal. For example, in the production of ready-to-drink tea, fruit juice drinks and similar sugared or acidic liquids. GEA aims to offer the customer the best possible solution with a broad portfolio and expert advice, depending on the existing conditions and requirements for the valve technology: "GEA valves are designed to adapt to the products and processes and not the process control of individual valve types being offered."
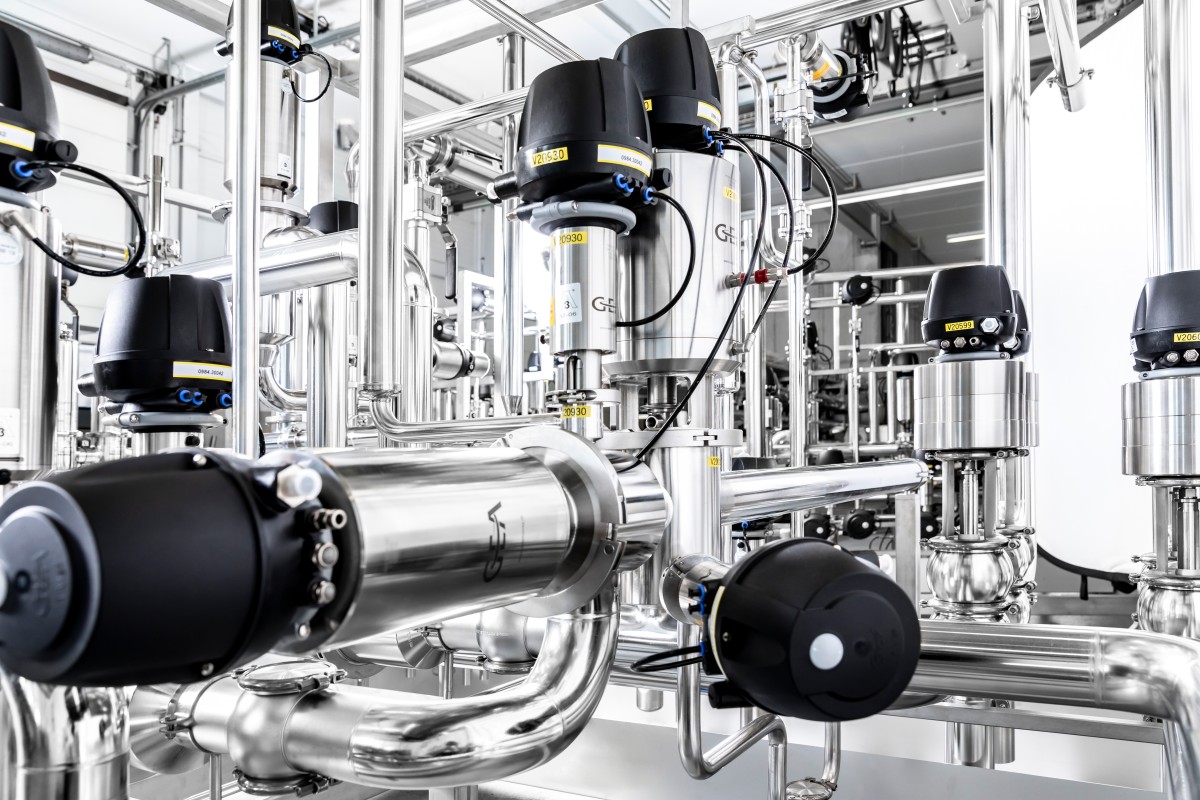
©GEA
Safety first
GEA is not only a pioneer in the development of valves based on stainless steel bellows technology, but also in double-seat valves in hygienic and aseptic design. Thanks to an integrated sterile chamber, aseptic double-chamber valves guarantee a mix-proof shut-off between two incompatible material flows in the process systems. These often occur at the transfer point between two main system components, for example at the interface between the UHT and the sterile tank.
Different process areas are often subject to different cleaning cycles due to the stress they are subjected to. If an automatic CIP cycle is currently taking place in one line, it should be ensured that production can continue in the other line without any problems. In this case as well, a metal bellows ensures that nothing can enter the product-carrying process area from the outside. With double chamber valves, there is also the sterile chamber in between, which is kept sterile with an application of hot steam. The double protection provided by the two valve seat seals and the additional sterile medium, together with a controlled overpressure, would prevent the mixing of different media even in the event of a defective seal.
Depending on the complexity of a system, double chamber valves with one, two or even three integrated and individually operable sterile chambers are available. Each sterile chamber has an inlet and outlet valve with independent selection of the rest position. The outlet can be fitted with a temperature sensor for process monitoring. As the barrier is usually operated with steam, viscous or sugary foods tend to cause scorching and similar material damage. Closing the outlet valve therefore interrupts the active vapour cycle and operates the valve with a colder, sterile condensate barrier.
As a premium version of the double-chamber valve technology, the AXV valves with three chambers also enable continuous operation of the system. This enables maintenance to be carried out on one side while production continues on the other.
Current status and outlook
Aseptomag® bellows valves fulfil the most stringent hygiene standards. Design guidelines such as those of the EHEDG and 3-A are part of the design process for component developers. The modular design consisting of a housing, inner section and drive also simplifies maintenance: Users simply release the clamp that holds the components together, allowing them to remove the drive and inner section and replace wearing parts such as seals and bellows as required. On request, GEA will also provide new customers with information on maintenance intervals as a recommendation. Regardless of this, customisation to individual process requirements is possible, such as valves made of special materials or in a special design.
With regard to the control system, according to product manager Bär, the use of digital control heads directly on the valve is becoming increasingly popular. The valves could be seamlessly integrated into an automated process plant using GEA's own control heads (T.VIS®) with minimal cabling - all in view of the fact that dozens of valves are usually required in such plants.
For additional information, go to: