3D Printing in the Food Industry
Layer by layer to the finished component
Together with robotics, digitalisation and machine learning, 3D printing is one of the major topics of the future. In this process, also known as additive manufacturing, a 3D model created using CAD is converted into two-dimensional layers, which are then applied one after the other during printing. The advantages of the process lie in the rapid realisation of innovative ideas, the freedom of design and the fact that it is largely geometry-independent - and this with a reduced use of resources, as hardly any waste is produced during manufacturing.
Disruptive technology shows its advantages especially in bionic lightweight structures, which are difficult to realise using traditional production methods such as CNC milling or turning. For example, honeycomb or grid structures are particularly suitable. They not only impress with their high stability, they are also significantly lighter in weight than solid components - both aspects that Reinhard Ortner, production technologist at Krones in Neutraubling, is concerned with. One example of this is a 3D-printed can turner that is used in Krones' filling machines. Its function: Turning beverage cans that pass through it by 180 degrees. Previously elaborately manufactured in stainless steel, Krones now relies on the Jet Fusion 5200 3D printer from HP.
Ortner, who heads the Additive Manufacturing division, is convinced: Additive component manufacturing offers many opportunities for mechanical engineering. With 3D printing, extremely small quantities can be realised cost-effectively, for example when producing prototypes. The technology is also interesting for the supply of spare parts for older machines, as the components no longer need to be kept in stock. Instead, they can be reproduced at short notice after design adjustments without the need for a specially made tool. Food manufacturers benefit not only from rapid availability, but also from components that are tailor-made for their machines - without any complex supply chains.
The can turner from the printer
One challenge is quality assurance. Often only insufficient measurement methods and standards are available for both the additive manufacturing processes and the components produced. This meant that various factors had to be taken into account when realising the 3D-printed can turner, as Krones' filling lines process up to 130,000 cans within an hour. "Every installed part must meet the high performance requirements of the system. In addition to stability, this also includes the elasticity and resistance of the material to cleaning agents," explains Ortner. The development team had to analyse a large number of points, such as the kinematics, i.e. the optimum motion sequence of the beverage cans during turning. "Added to this were tribological properties, i.e. the frictional behaviour between the cans and the material," adds Andreas Neuber, development engineer with a focus on additive manufacturing at Krones.
However, the calculations revealed the advantages of the additively manufactured can turner: The use of the 3D printer made it possible to reduce the weight of the component by around 80 percent. Another advantage: The ideal can guide can be reproduced as often as required and easily adapted to new container formats, as the lower weight means easier handling when converting the filling systems, for example when changing from a 0.5 litre can to a 0.3 litre can. This is now possible without tools.
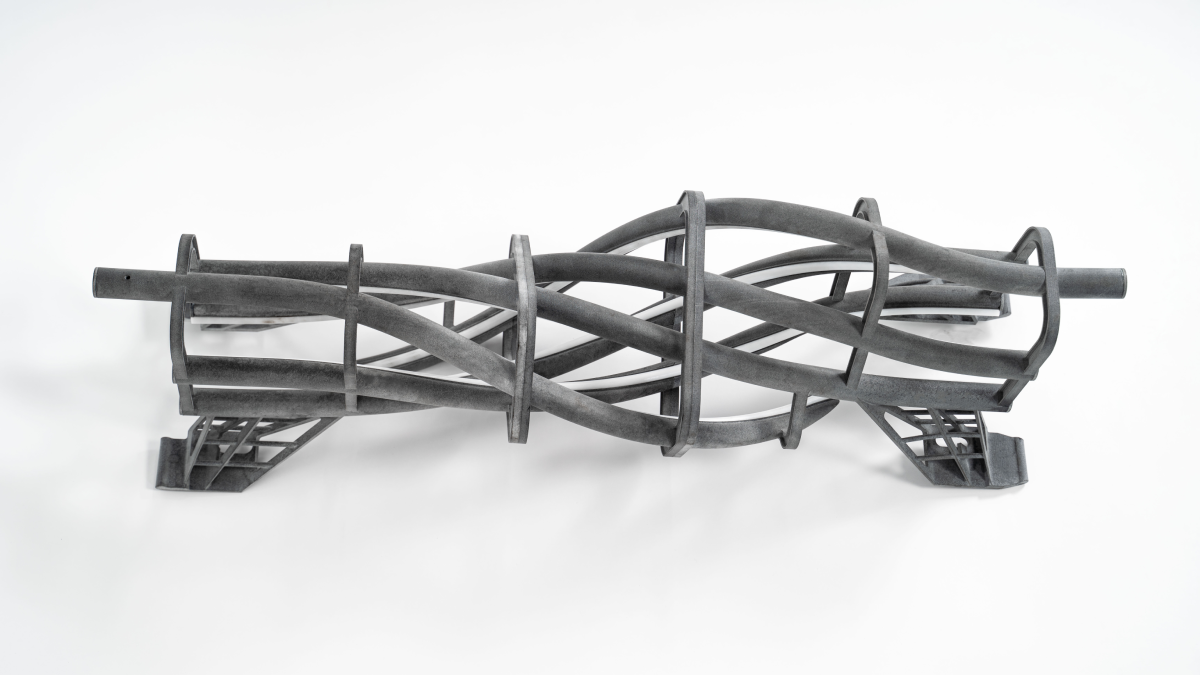
The 3D-printed can turner from Krones can turn up to 130,000 cans 180 degrees in one hour for filling. © Krones
Printed sensors for greater precision
For many experts, Multi Material Jetting (MMJ) technology is the next step in additive manufacturing. With up to six print heads, and therefore up to six different materials, the latest generation of high-tech printers achieves component accuracies of 70 to 100 micrometres. With an additional laser module that removes material, polishes or structures the surfaces during 3D printing, roughness of less than one micrometre is achieved. This eliminates the need for time-consuming post-processing of the components. This enables manufacturers to further optimise their production in terms of time and costs. AI methods for quality assurance like defect detection and automatic adjustment of process parameters during printing also contribute to this. This allows functionalised components or entire assemblies, for example with integrated sensors or actuators, to be printed within a process.
Thanks to the new variety of materials available, there are virtually no limits to creativity. Materials with defined properties can be produced and combined. These include electrically conductive and electrically insulating, dense and porous, hard and ductile or magnetic and non-magnetic. One example of an innovation that the Fraunhofer Institute for Laser Technology ILT is working on is the seamless integration of sensors during the additive manufacturing process. With the help of 3D structure printing processes such as Laser Powder Bed Fusion (LPBF), printed sensors can be integrated directly in the components as they are created. This not only enables the precise positioning of sensors for sophisticated condition analyses (condition monitoring), but also protects these sensors from mechanical environmental influences. "The geometry of the sensors can be customised depending on the component. In the future, even more functional elements such as integrated heaters are conceivable," says Samuel Fink, Group Manager for Thin-Film Processes at the Fraunhofer ILT.
Tools on a pay-per-use basis
Despite all the enthusiasm about future technical possibilities, food producers are demanding one thing above all: Flawlessly functioning solutions to turn new ideas into concrete products quickly and cost-effectively today. At Anuga FoodTec 2024, the Schubert Group showed what it takes to turn a 3D-printed object into a ready-to-use tool for a packaging machine. The company based in Crailsheim, Germany no longer builds any packaging machines without size parts printed in-house. For example, the Heinrichsthaler dairy uses a Schubert cartoner for packaging its grilled cheese rounds with robots equipped with appropriate vacuum cups. A Schubert in-house development is being used here: the PARTBOX, an industrial-grade 3D printer.
There are many advantages to the customer printing components for the packaging process in-house: optimally adapted robot tools for all conceivable products, no time-consuming transport of new size parts, quick replacement of defective tools and the ability for the customer to produce size sets for modified products itself. "We’re convinced that components should be produced when and where they are needed," explains Conrad Zanzinger, Technical Director at Schubert Additive Solutions. The company was founded by the Schubert Group to enable customers to receive the digital production data for the parts they order and produce them using additive manufacturing on a pay-per-use basis.
With the PARTBOX printer, it was important for Schubert Additive Solutions to design a solution that can be used without a great deal of expertise. This means that not only parts for Schubert packaging machines can be produced, but also those of other machine manufacturers. If the customer has a Schubert machine, they can call up the print jobs for the associated parts on the PARTBOX streaming platform. If new products are to be processed on the machine, Schubert develops suitable size parts and then uploads the print job. "This makes it very easy for the customer to print the part they need at their own company using our self-developed printer," says Zanzinger.
3D printing in hygiene-critical industries
All parts intended to come into contact with food must be certified accordingly. Schubert Additive Solutions also supplies the right printing material in the form of "PARTBOX Black" plastic. The difference to commercially available filaments lies in a polyamide optimised for the FDM (Fused Deposition Modelling) printing process. The material is food-safe and can be detected with a metal detector. It also exhibits good mechanical properties and high temperature resistance. This allows very smooth surfaces to be achieved in the printing process.
The examples show: 3D printing enables customised, tool-free production of complex geometries. A technology of the future, but one that poses challenges for use in hygiene-critical areas such as the food industry. With metallic 3D printing, such as laser beam melting, the resulting surfaces often do not have the necessary hygienic surface properties due to their high degree of roughness. The development and validation of special finishing strategies to perfect surfaces that come into contact with the product is another obstacle that needs to be overcome in additive manufacturing for the food industry in the coming years.
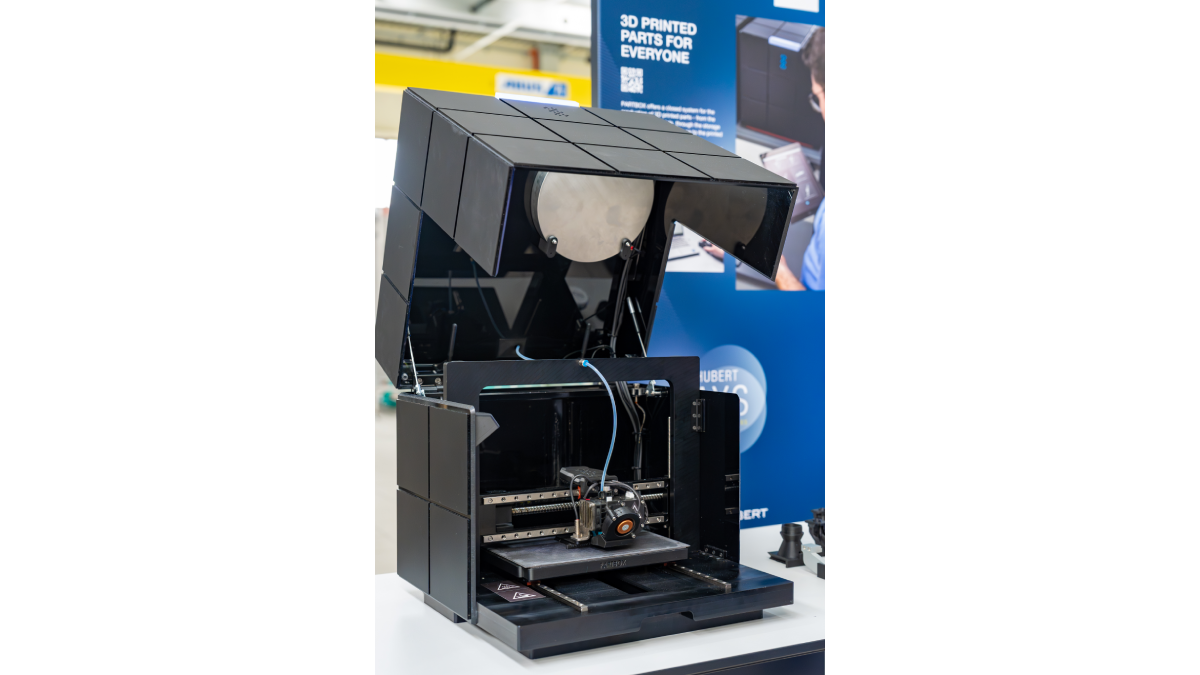
Producing 3D parts with a click: Print jobs can be started directly on the 3D printer via the PARTBOX streaming platform from Schubert Additive Solutions. ©Press4Process